
UTK Filament Tower
[Prof. Marshall Prado] ARCH 555: Spring–Fall 2019 Computational Design and Robotic Fabrication
Full list of those that made this project possible.
Awards and Press:
The Filament Tower is a design-build project focusing on the application of computational design to the built environment. It focuses on the utilization of robotics as a means to produce unique forms without the need to produce complex molds. The initial concept and design was developed by Professor Marshall Prado as a competition entry for the 2019 Exhibit Columbus University Design Research Fellowship. As 1 of 6 teams to be awarded the fellowship, Prof. Prado was able to lead a student design team in developing a strategy to robotically wind the 27 carbon and glass fiber composite components that comprised the 30 foot tall tower. Over the course of the project, interested students were able to participate in all aspects of the design development and construction. This included multiple visits to Columbus to engage with the site and complete construction/deconstruction, as well as representing the university during the fellowship presentation and the exhibition opening. During its 4 month installation thousands of people were able to view the tower as part of a city wide arts tour.
Because the tower was the first of its kind, the process and tools for its construction had to be developed. The first few months of the project consisted of material testing, winding frame iteration, tool development, winding syntax development, and design of the structural bases. We then went into prototype production of the components. This allowed us to fine tune our tools and processes to fluidly shift into full production.
My direct contributions consisted of:
Design/construction of site model for design presentation
Material testing
Development/fabrication of configurable winding frame
Tool development for frame positioning
Finalizing design and construction of the tempering chamber
Component winding and tempering
Component connection/process development
Exhibit installation
The image galleries below describe the process.
01_Design Presentation
02.1_Fabrication - Frames
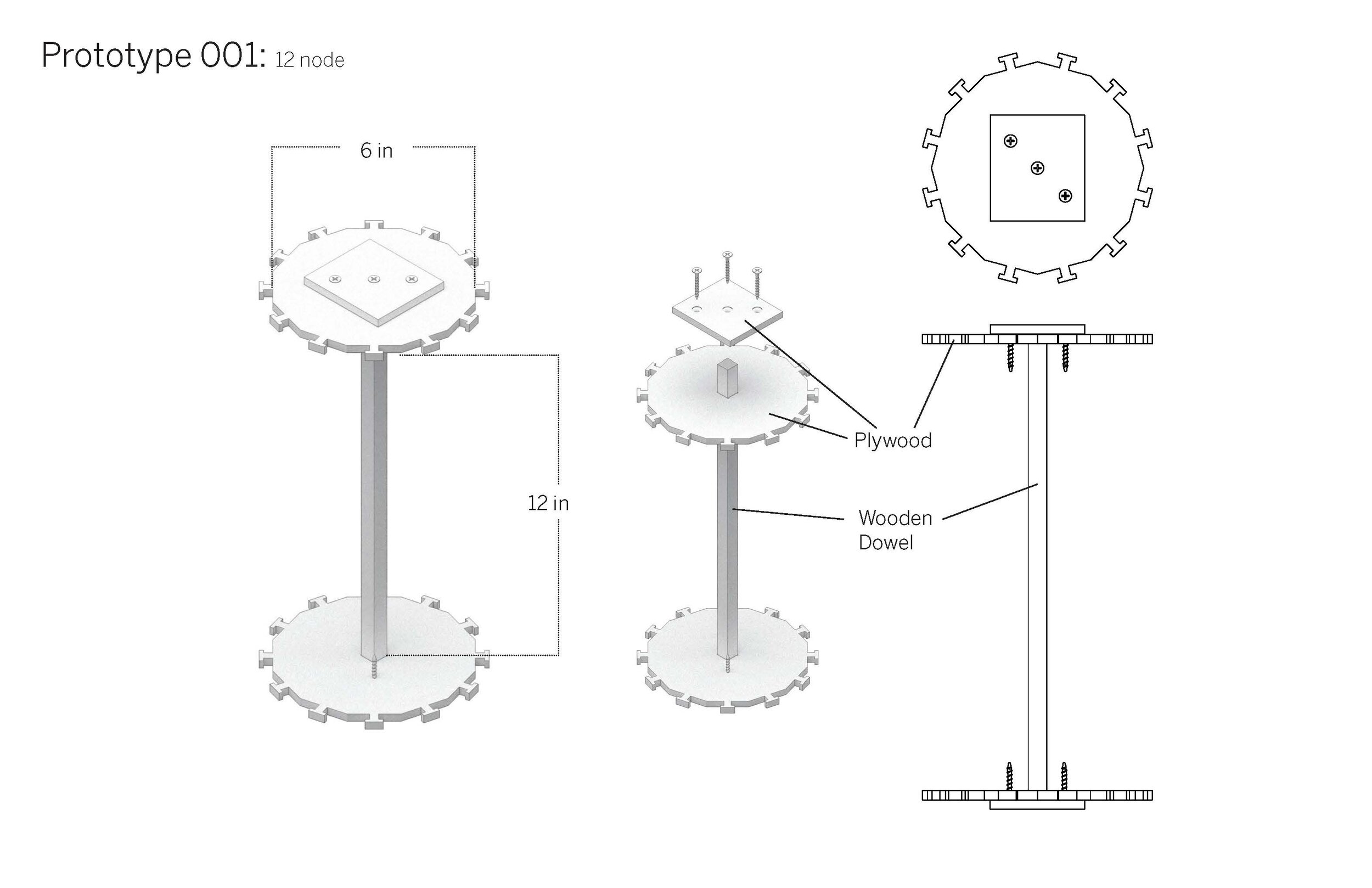
Building test frames for composite material strength testing.
Hand winding version 1 frame.
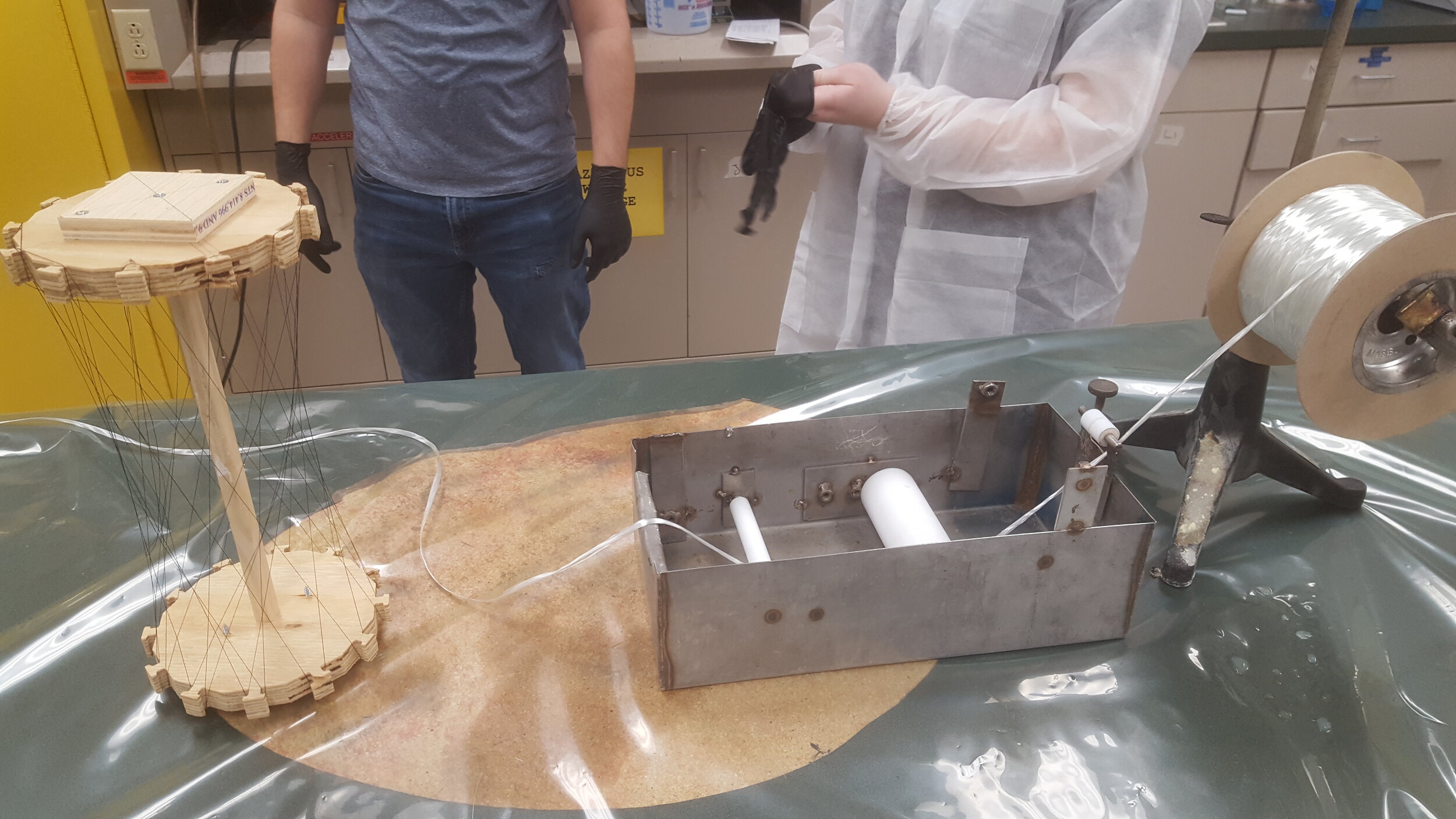
Prototype resin bath.
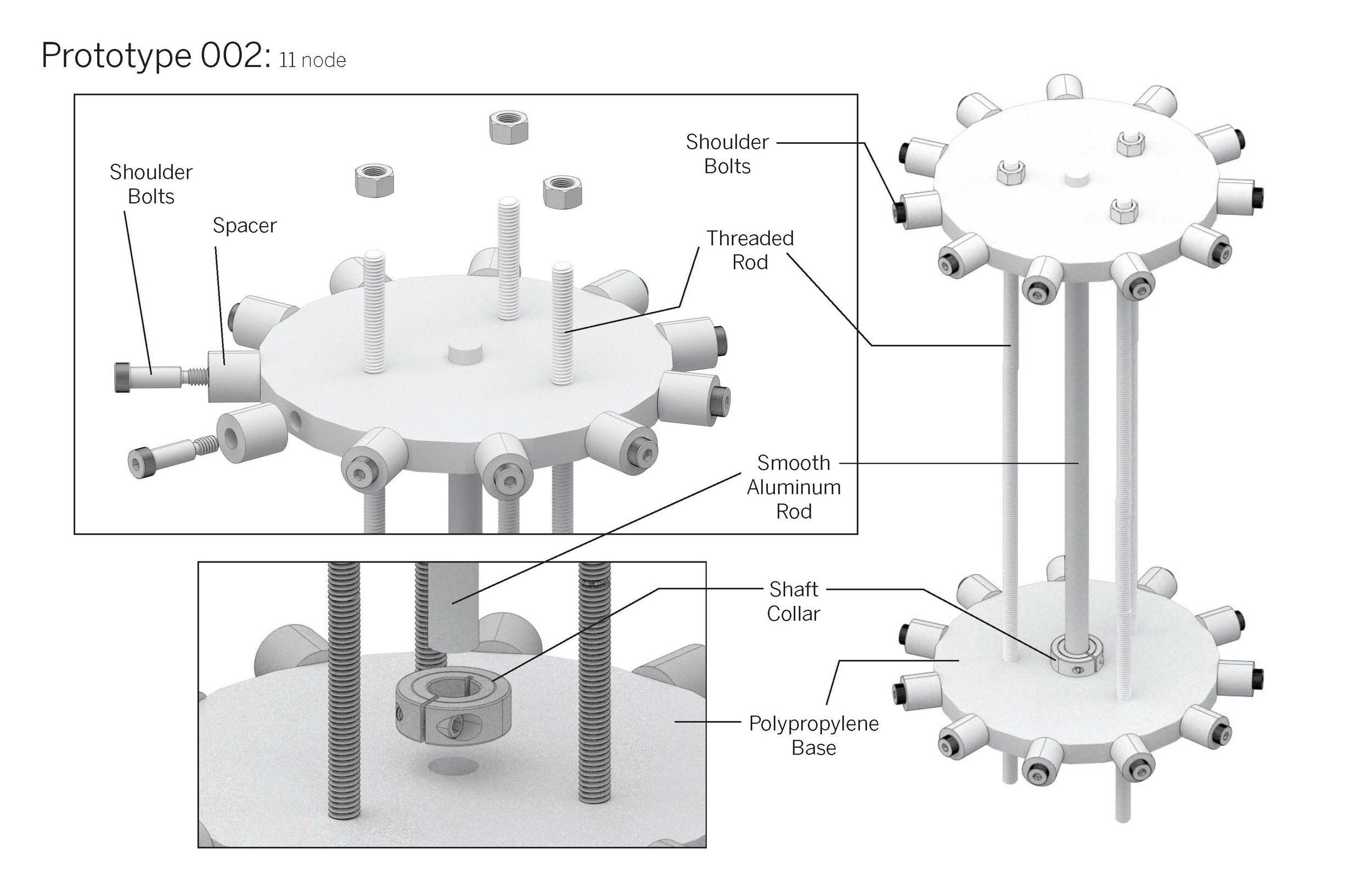
Second test frame prototype.
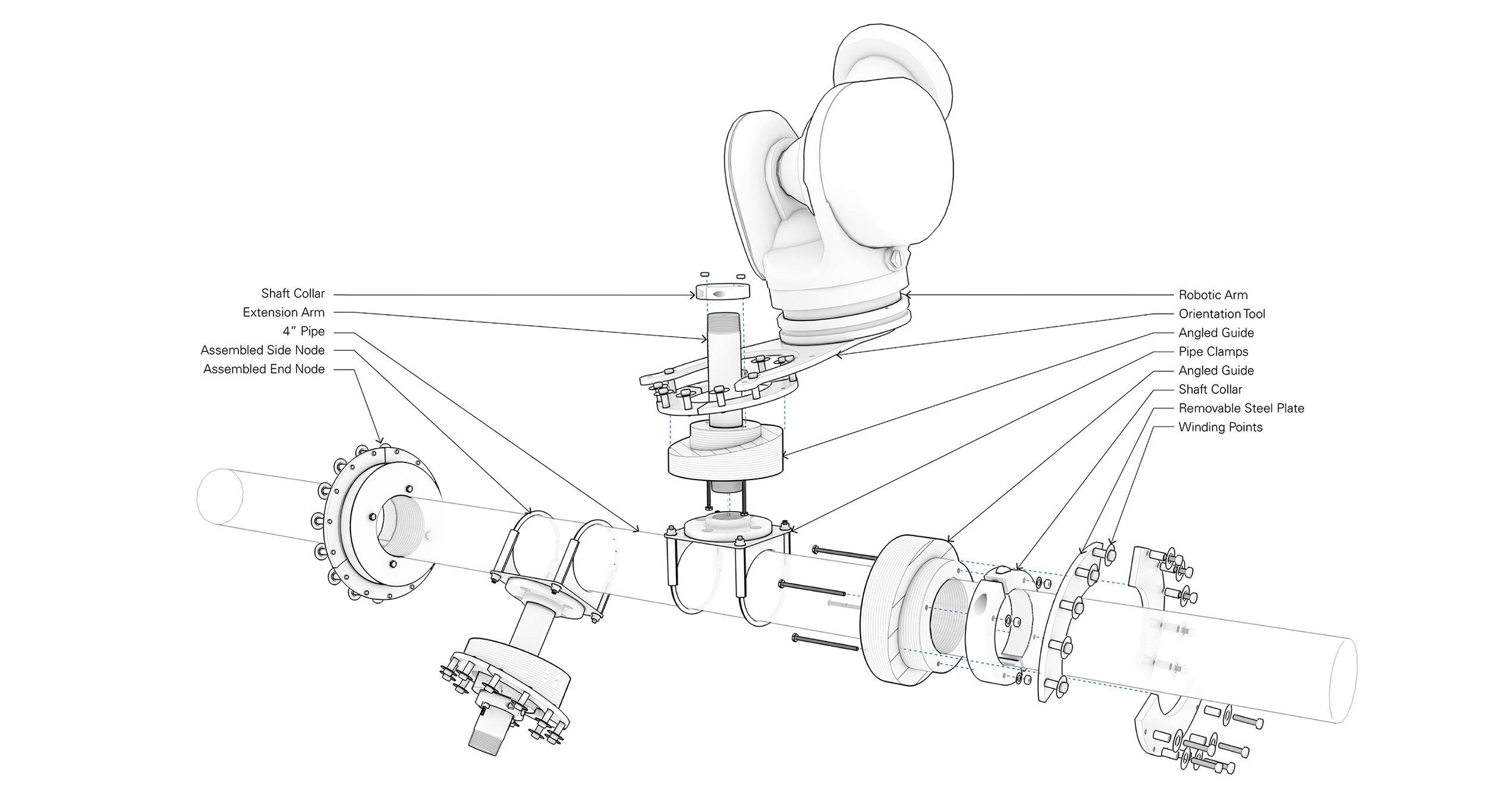
Design of the full scale winding frame and positioning tool.

The positioning tool needed to connect to both the large and small nodes without being removed from the robot.

Every connection between the nodes was unique. This required CNC milling over 100 connections to place winding nodes at the correct angles.
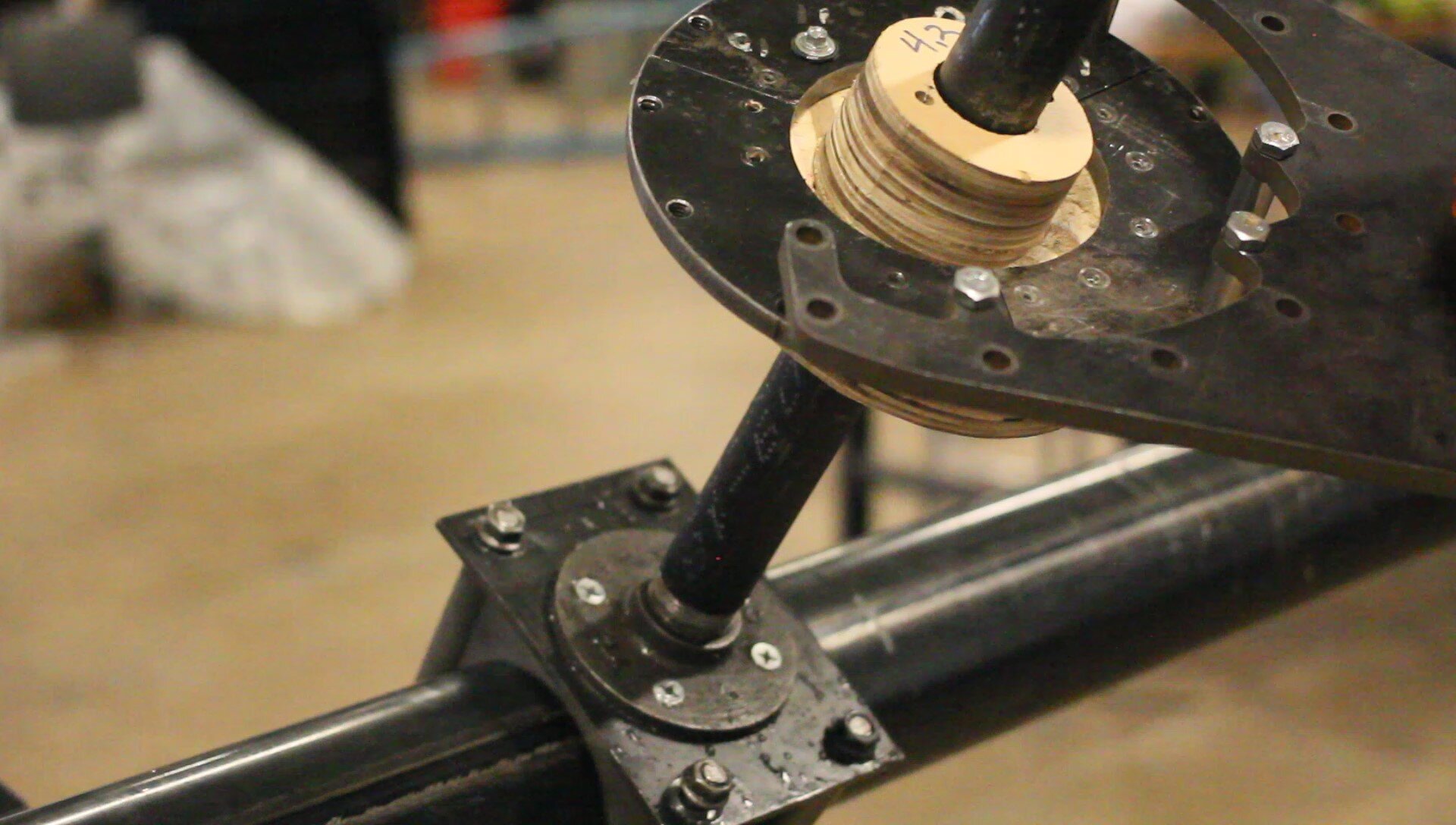
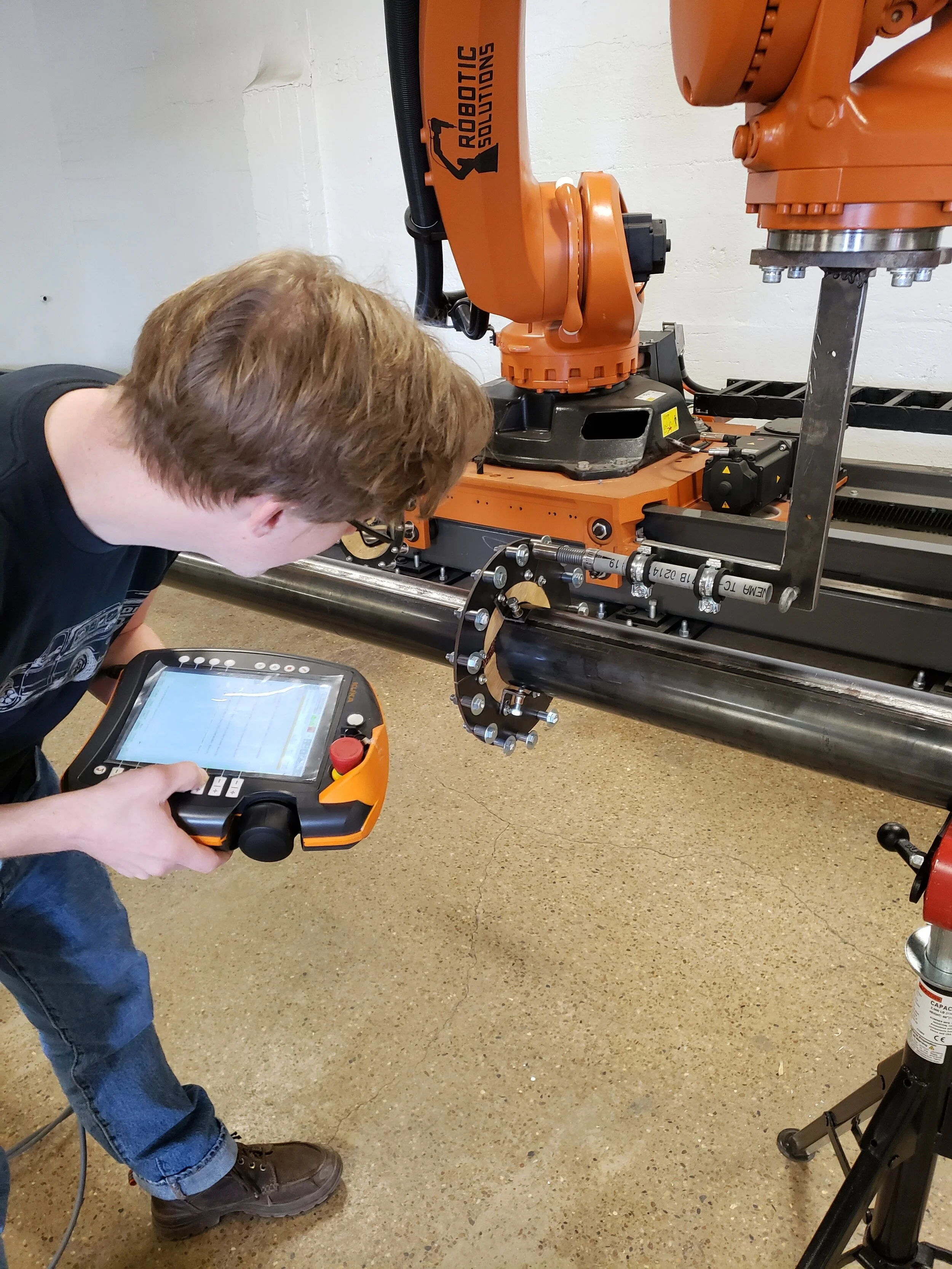
Making sure the nodes have been placed correctly on the frame.
02.2_Fabrication - Components

Fully wound component before being placed in the temper chamber.
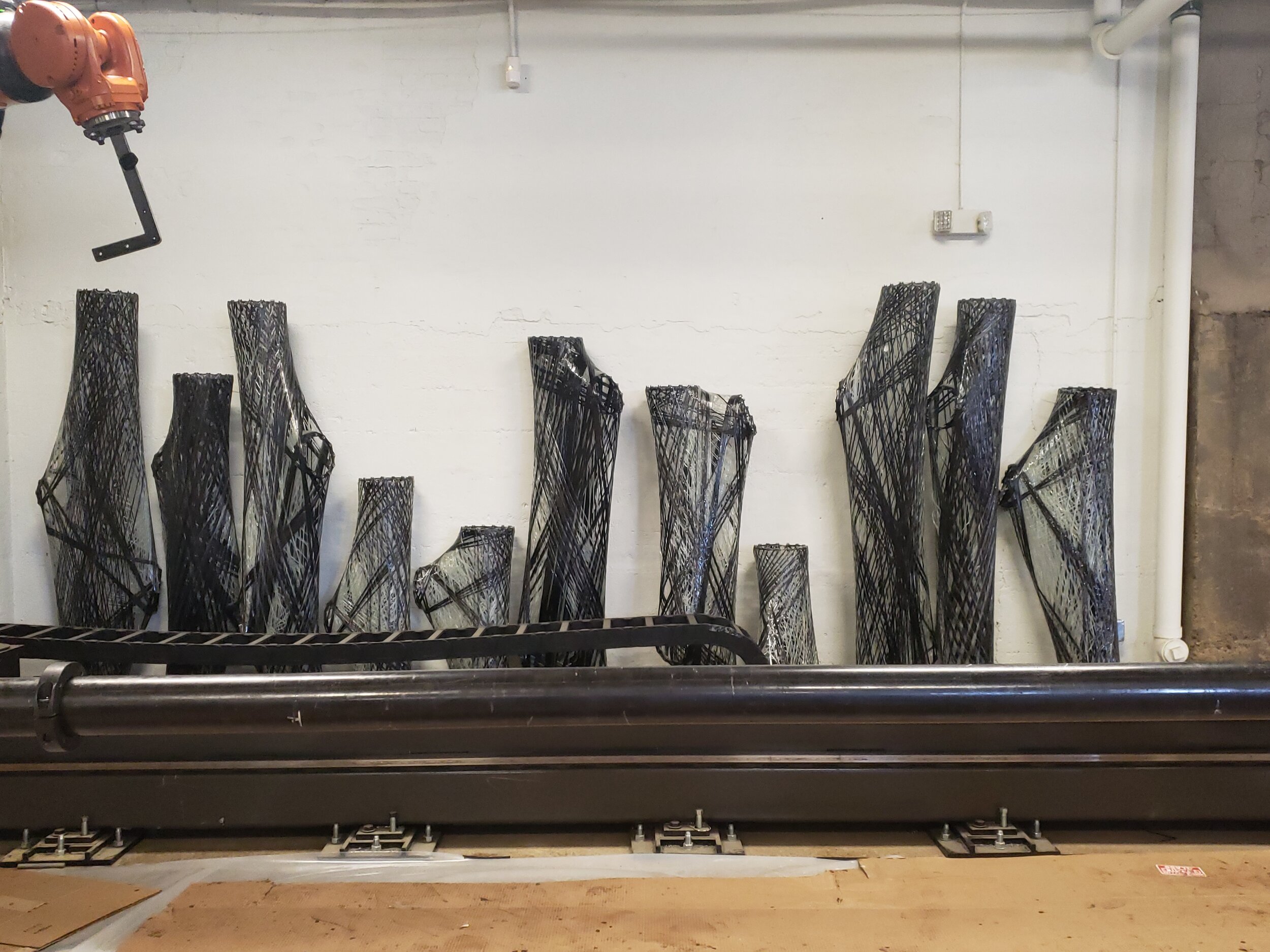
the frame system we developed was able to accommodate extreme range in size of the components.

The largest of the components was over 6 feet tall.
Winding tool used to place the fibers.
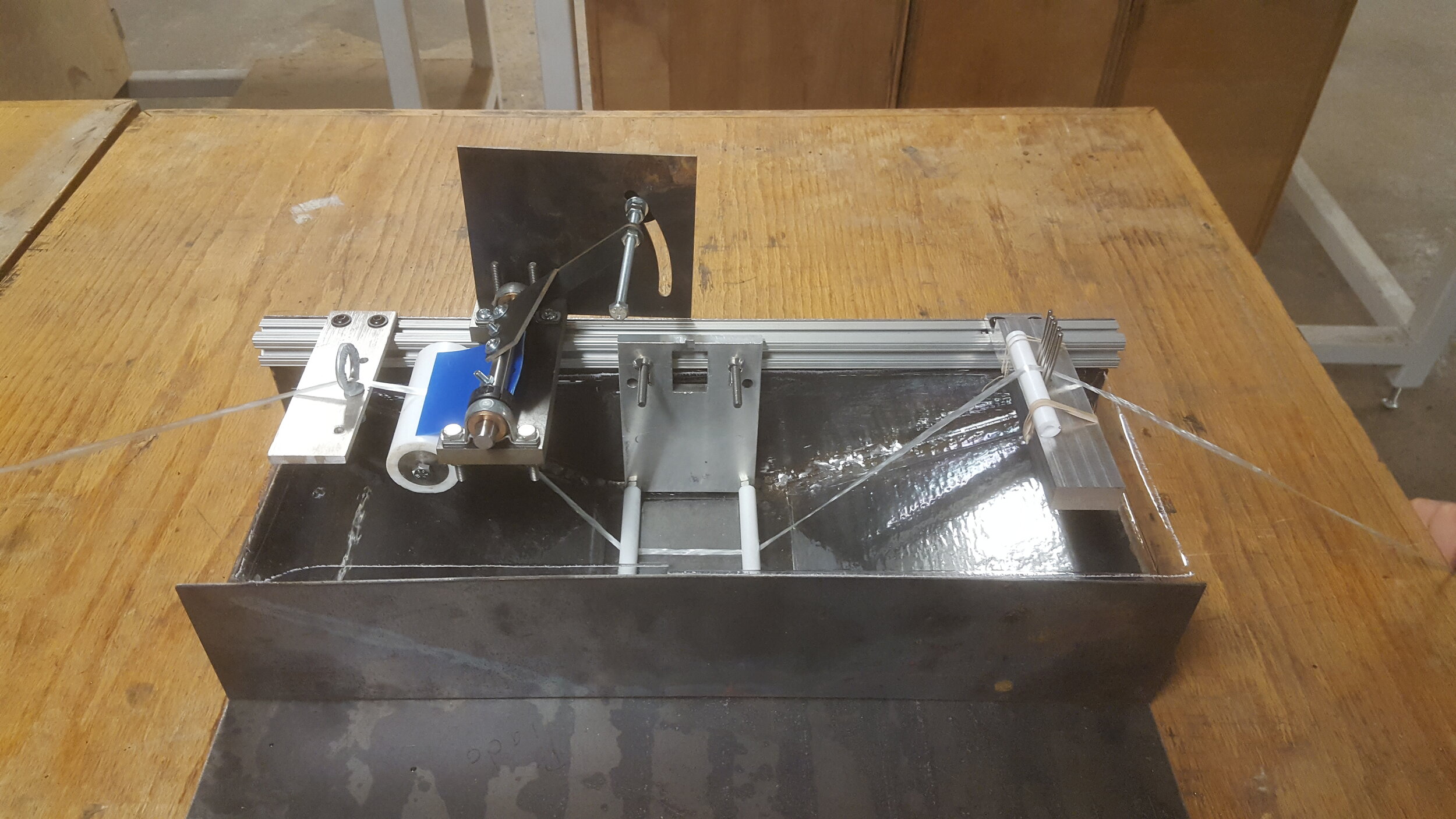
Second generation resin bath impregnates fibers with resin and removes excess material.
02.3_Fabrication - Heater

By post tempering the composites for 1 hour during the curing process we where able to increase the overall strength of the components.
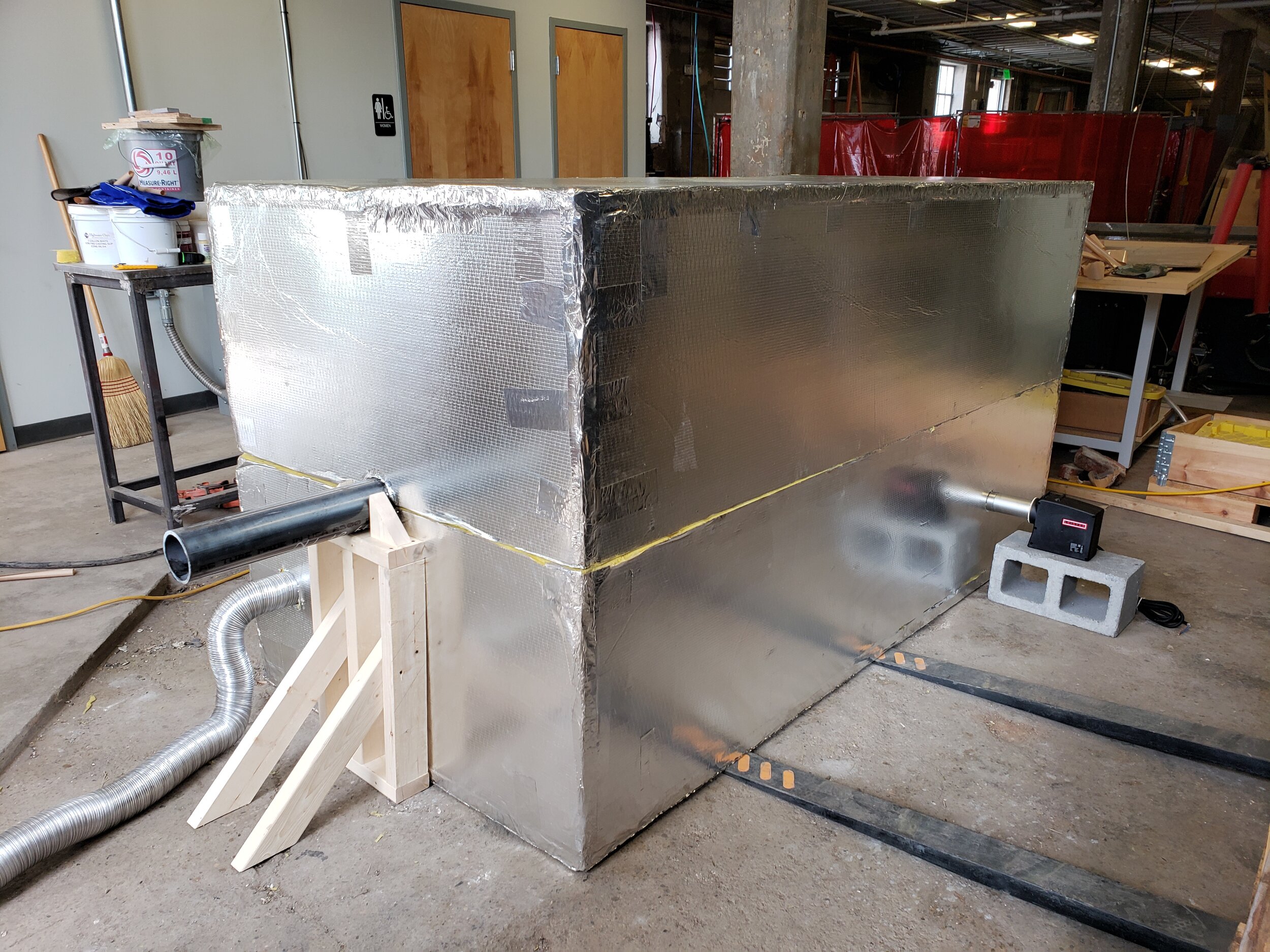
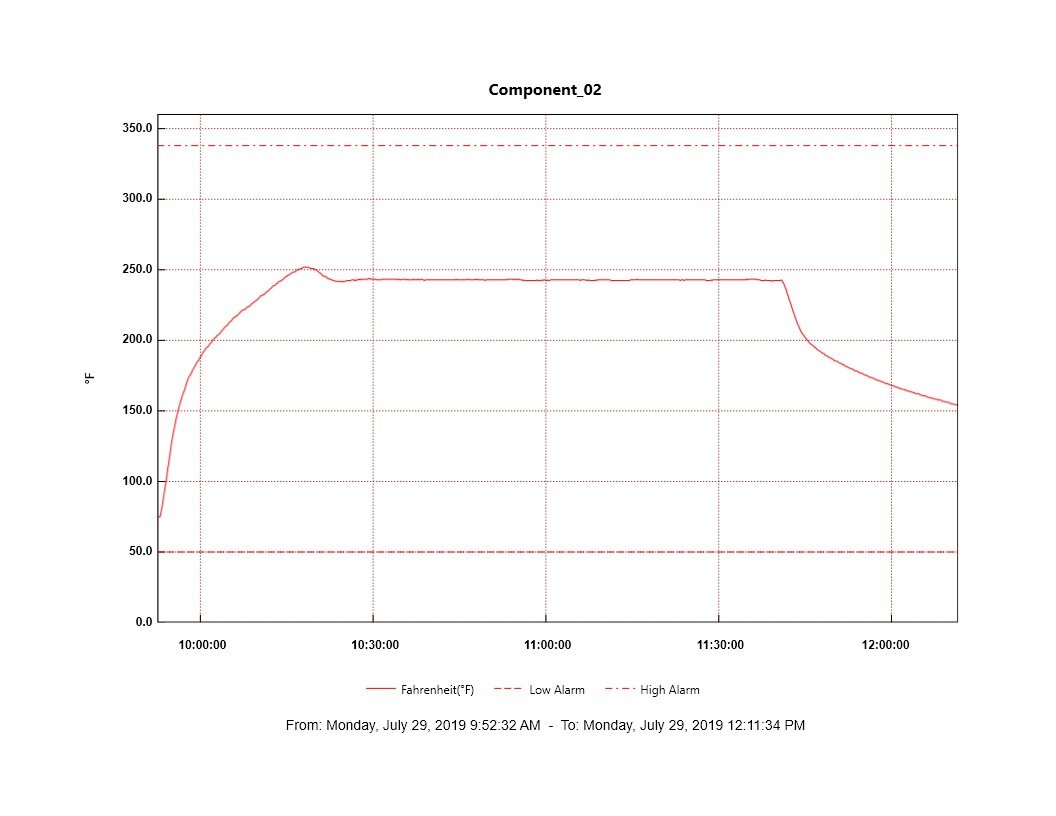
The heater had multiple thermometers to ensure that each component is kept at the proper temperature for the correct amount of time.
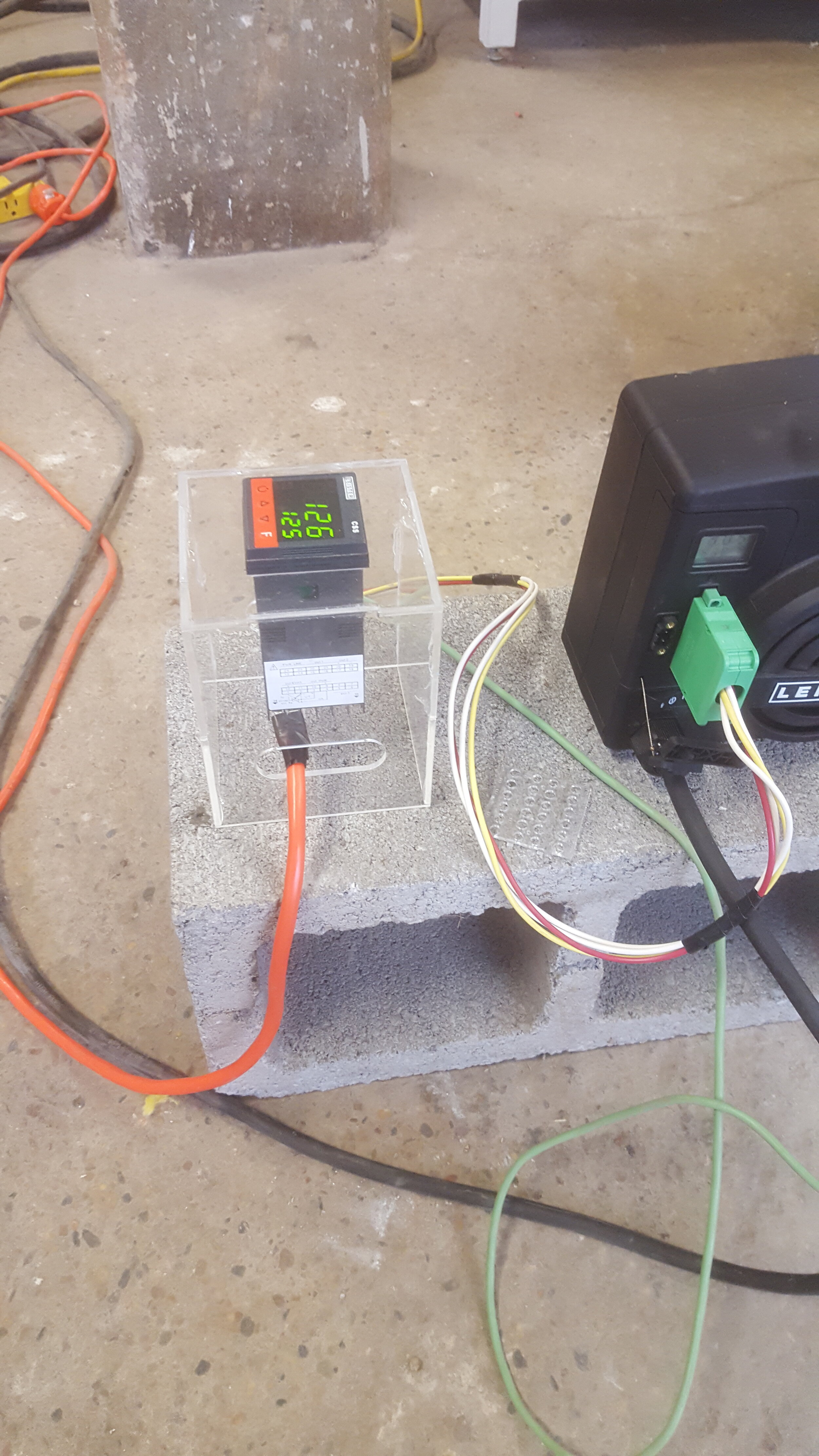
I wired our industrial heater with a regulating thermometer to keep the temperature consistent.
02.4_Fabrication - Bases
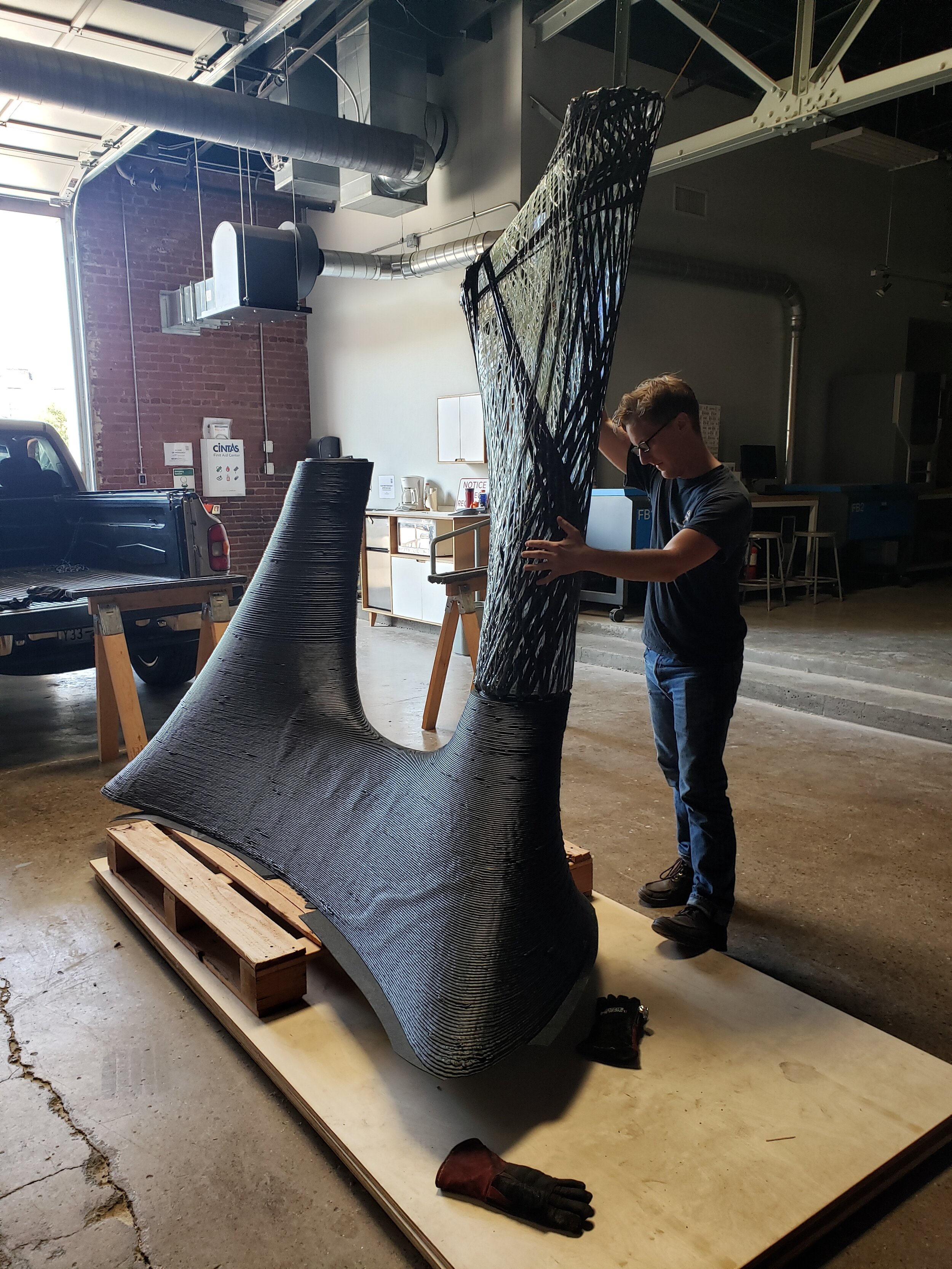
Finally getting to see what the components look like with the bases.
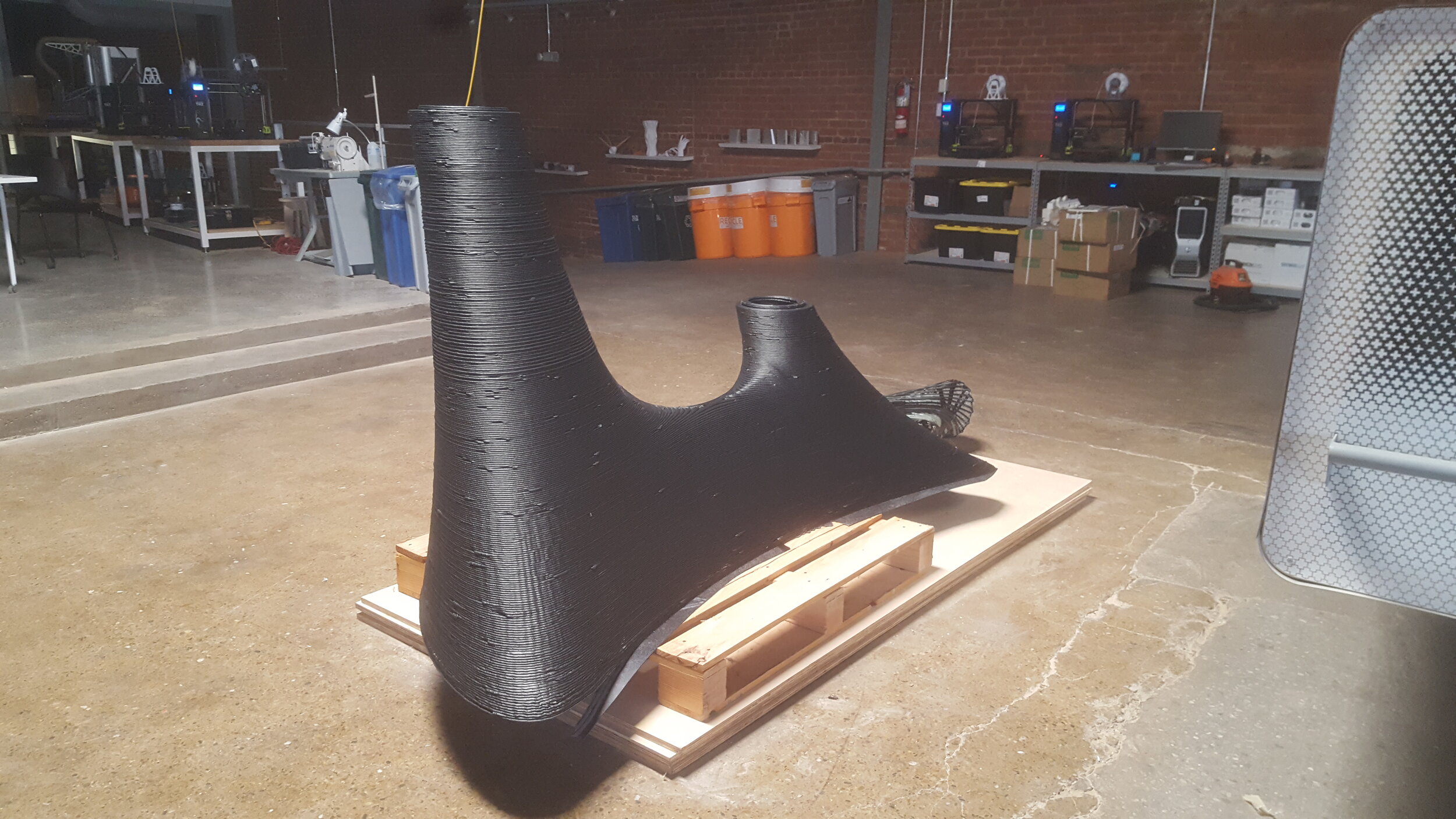
First base back to the FabLab
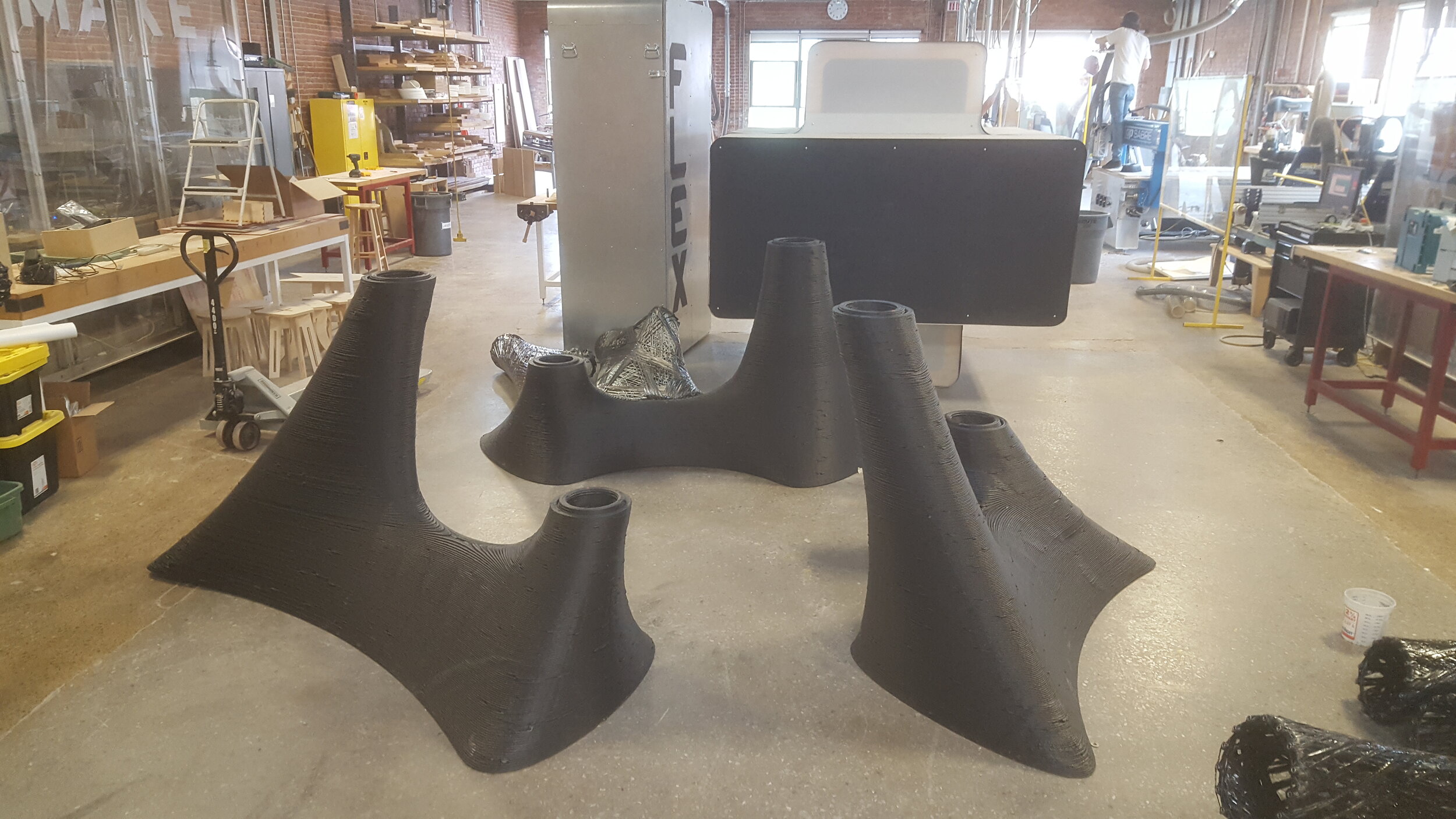
Getting to see the footprint of the tower.
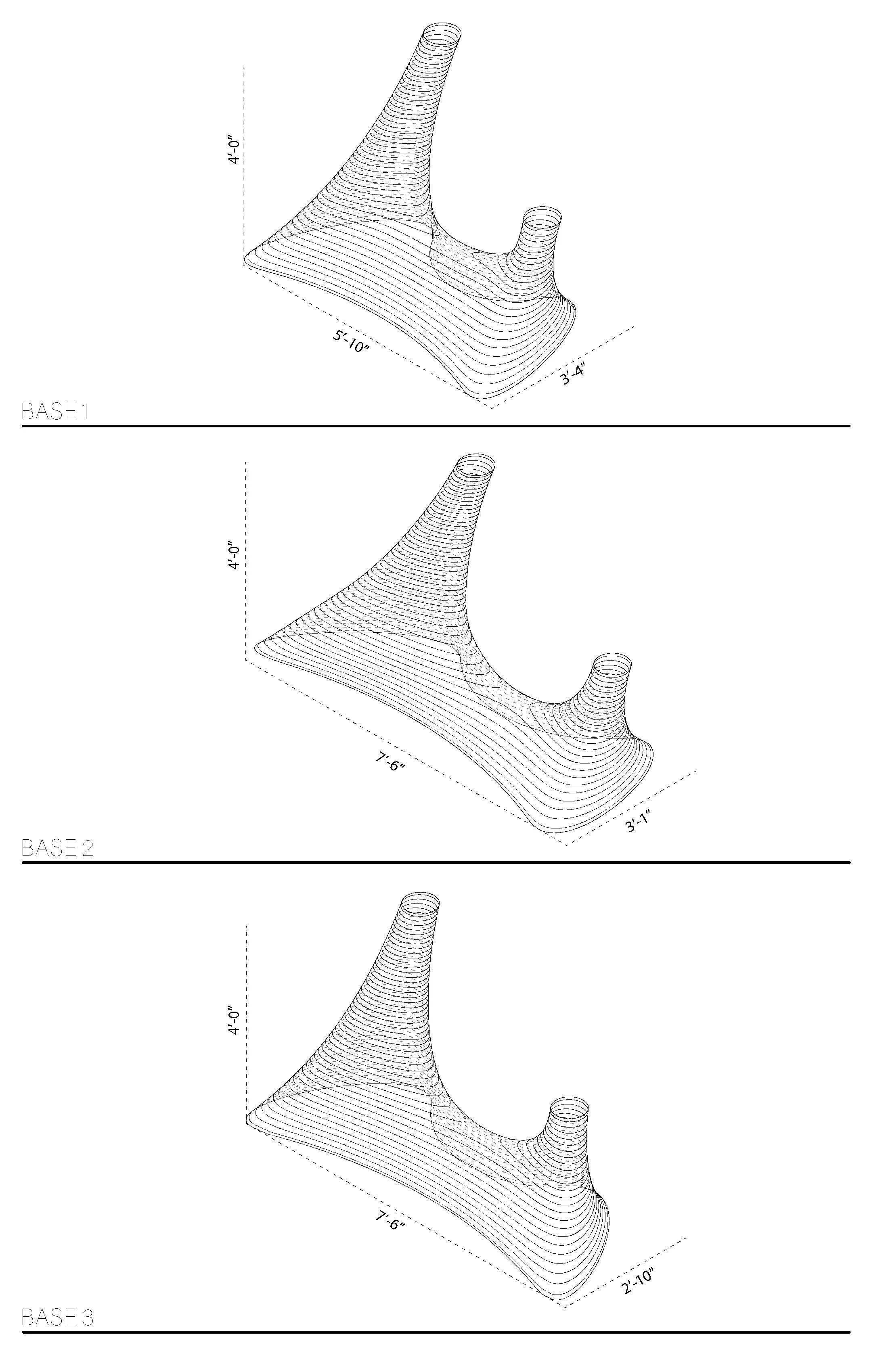
The development of the bases was done in conjunction with Oak Ridge National Labs. They coached our base team directly to help produce successful and strong 3D prints.
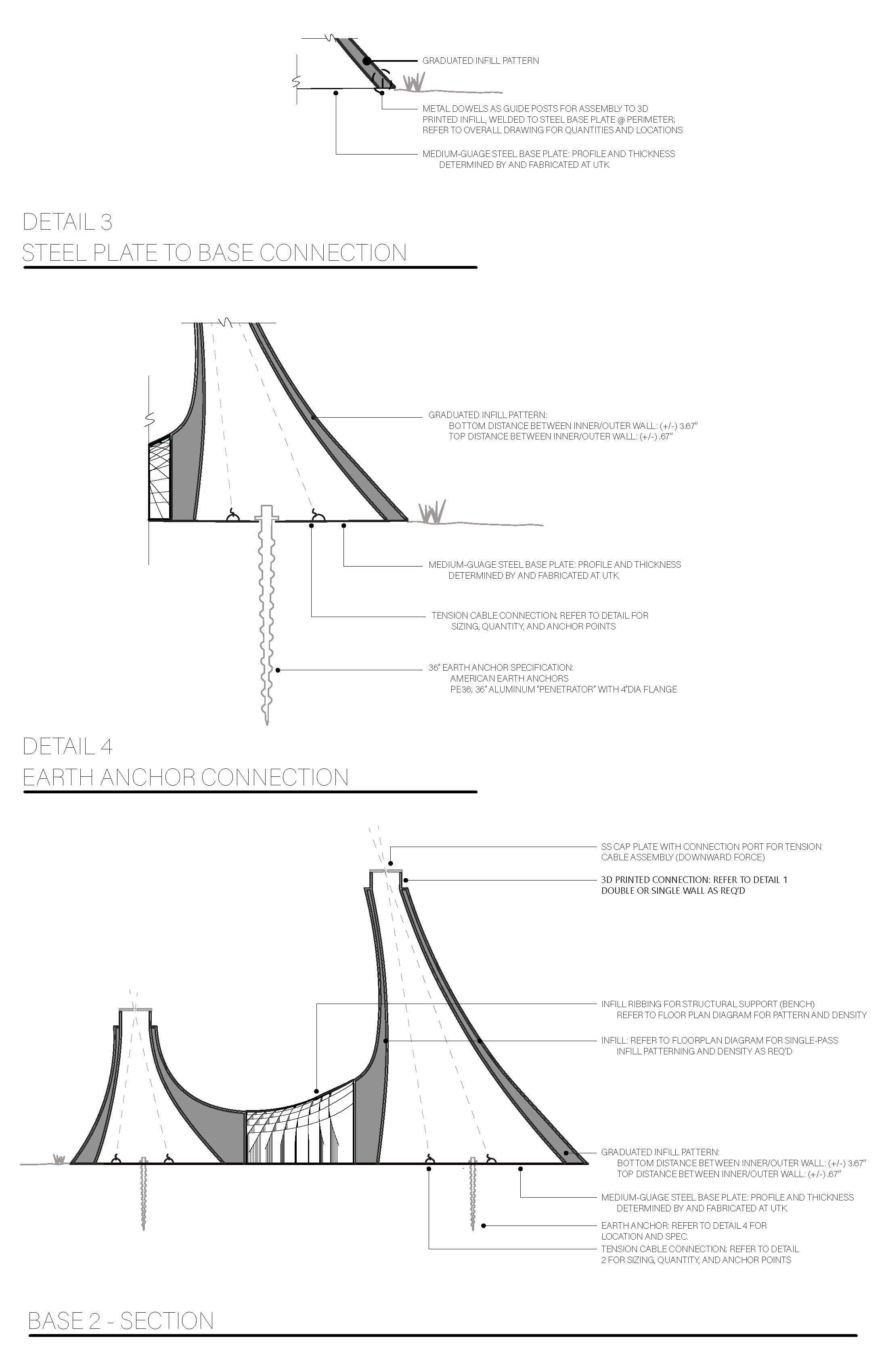
The base team developed a plan to post tension the bases to the large earth anchors needed for support.
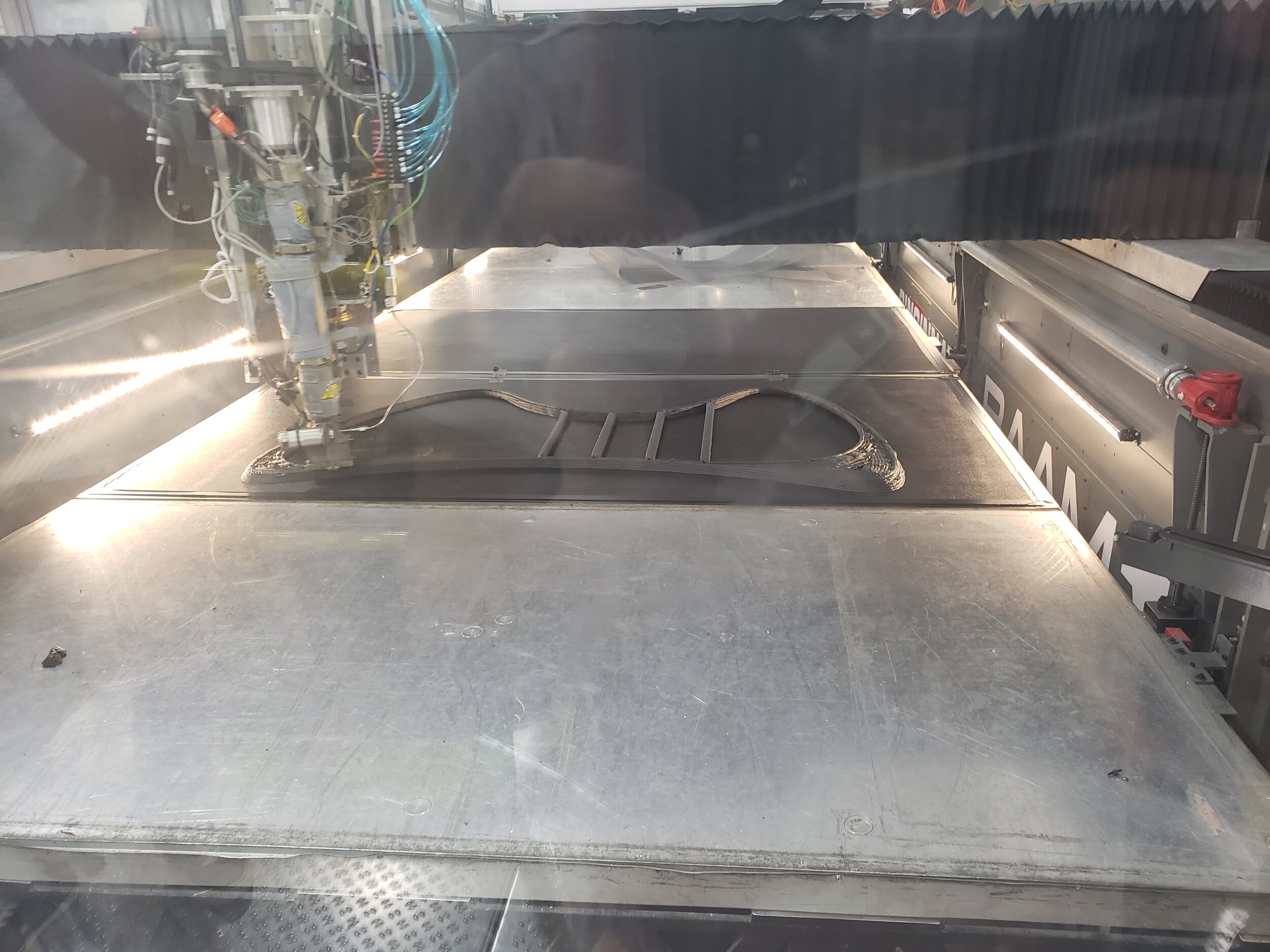
One of the bases being printed on ORNL's BAAM printer.
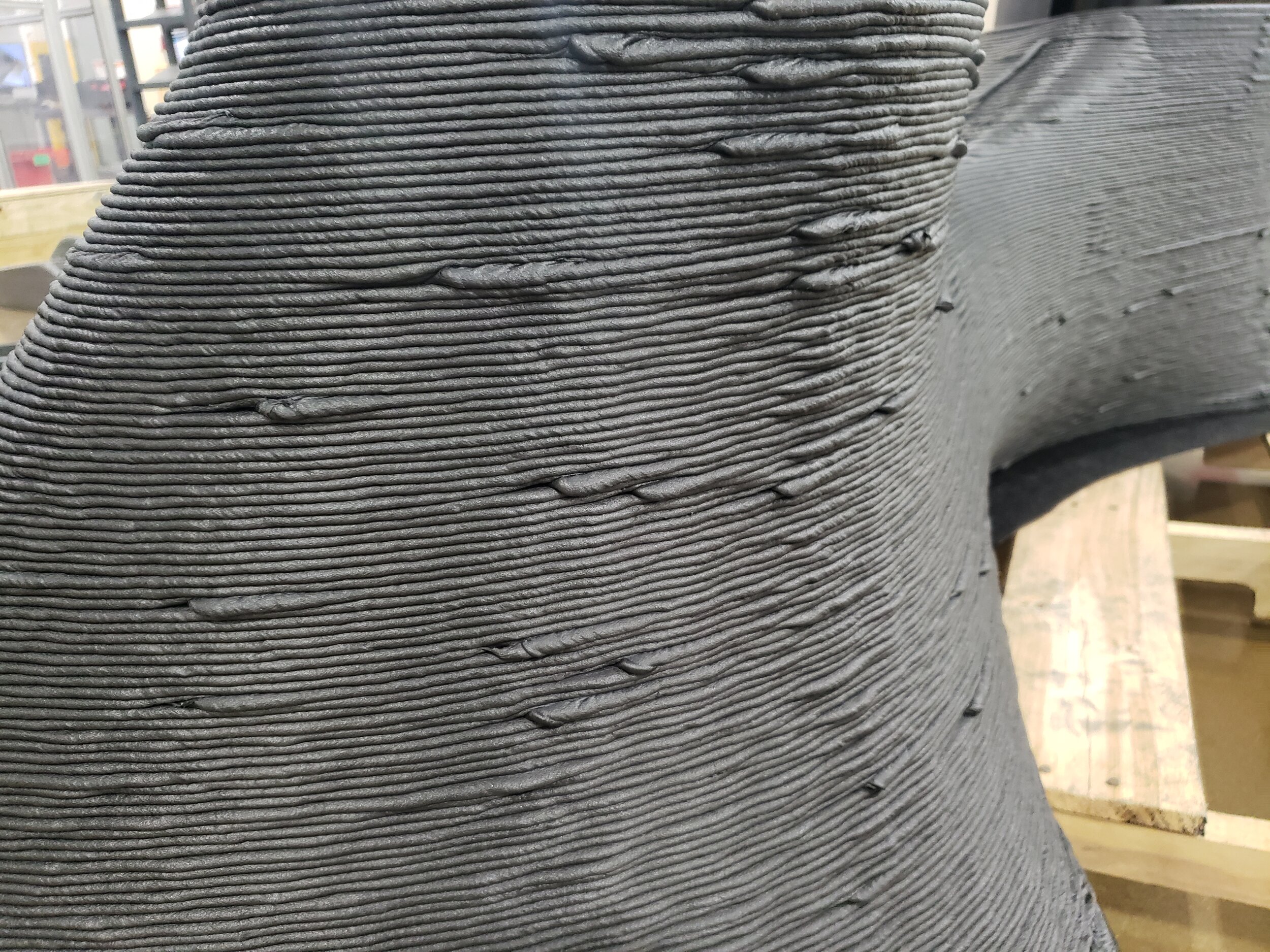
03_Installation
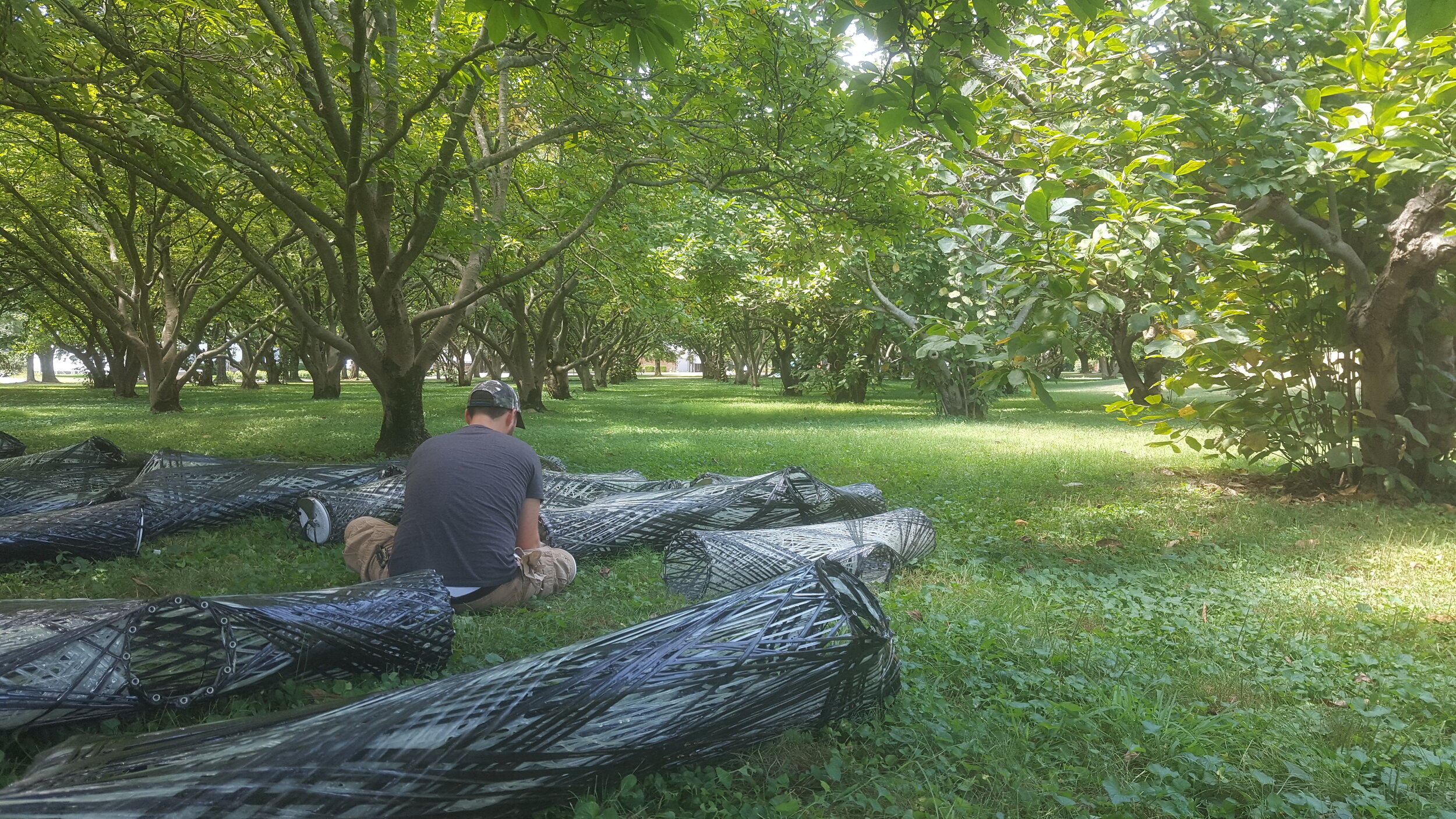
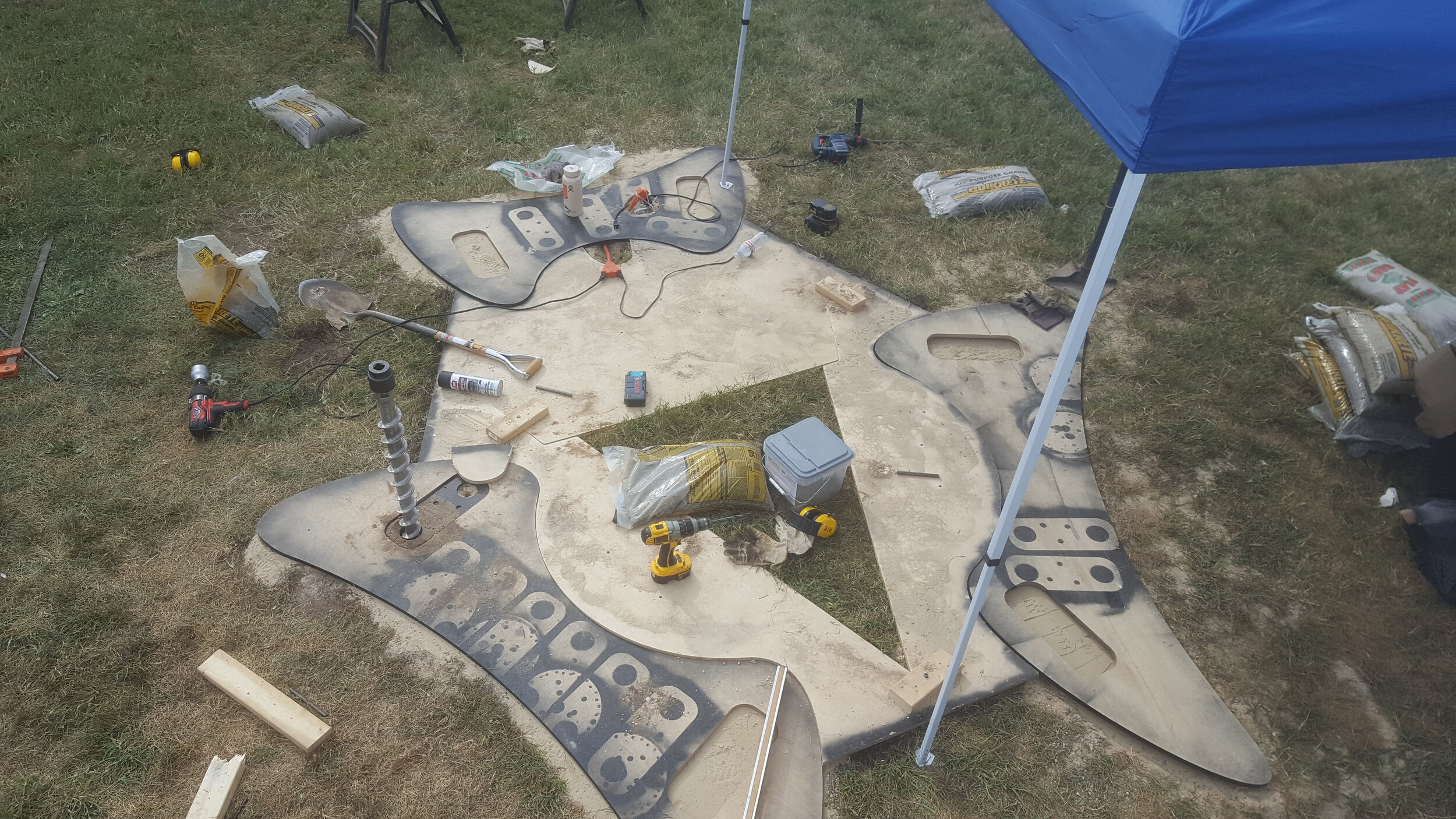
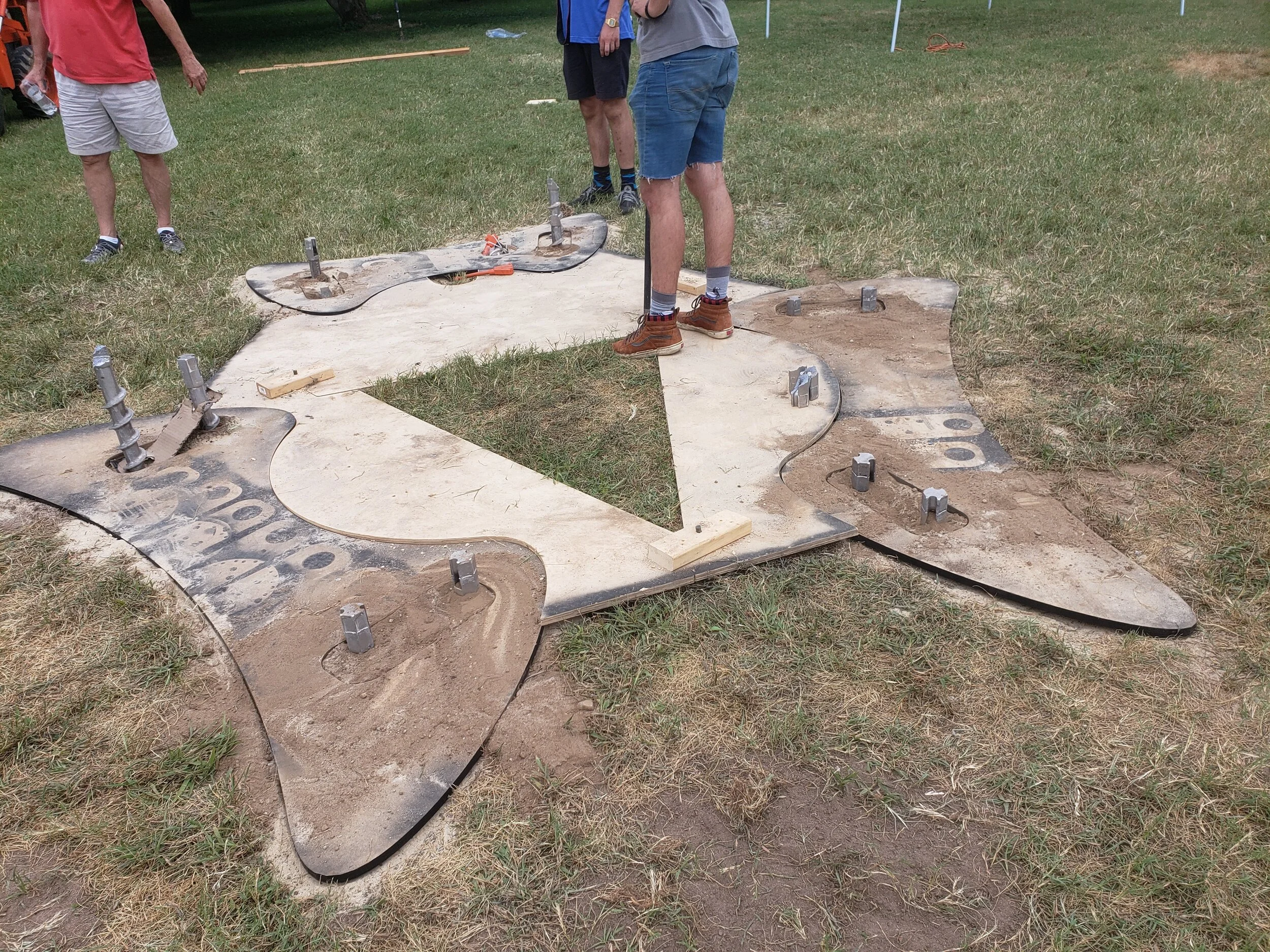
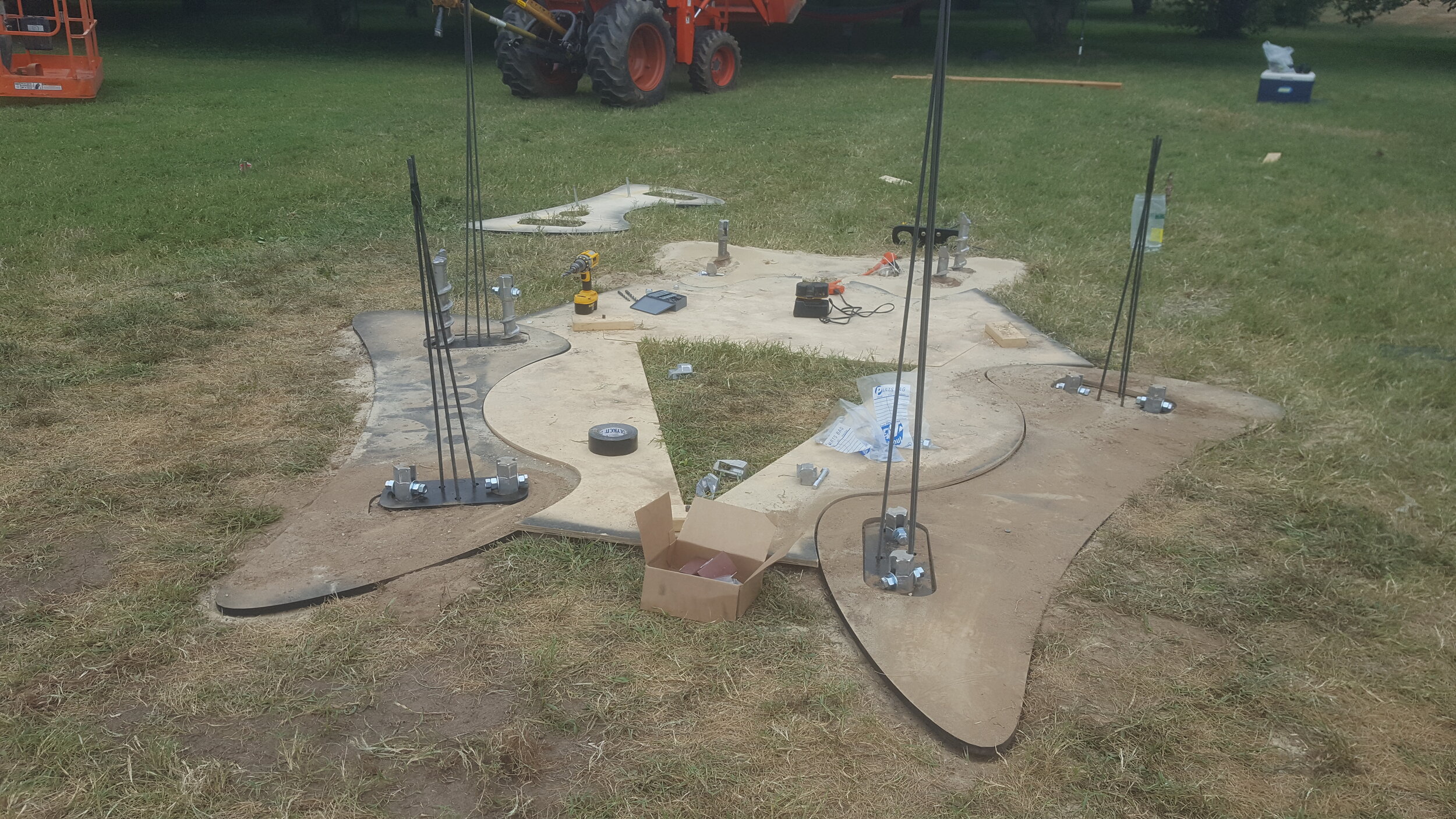
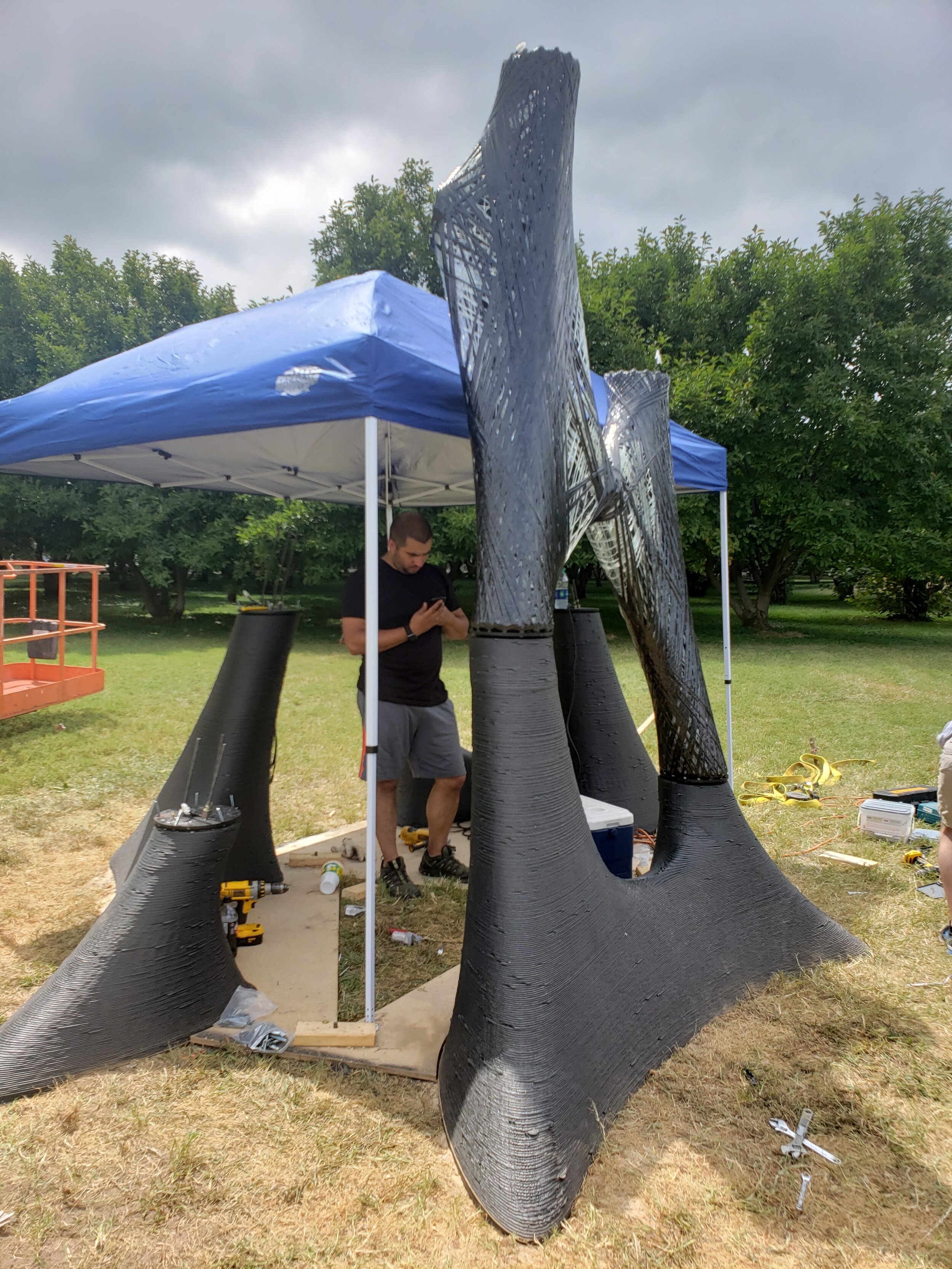
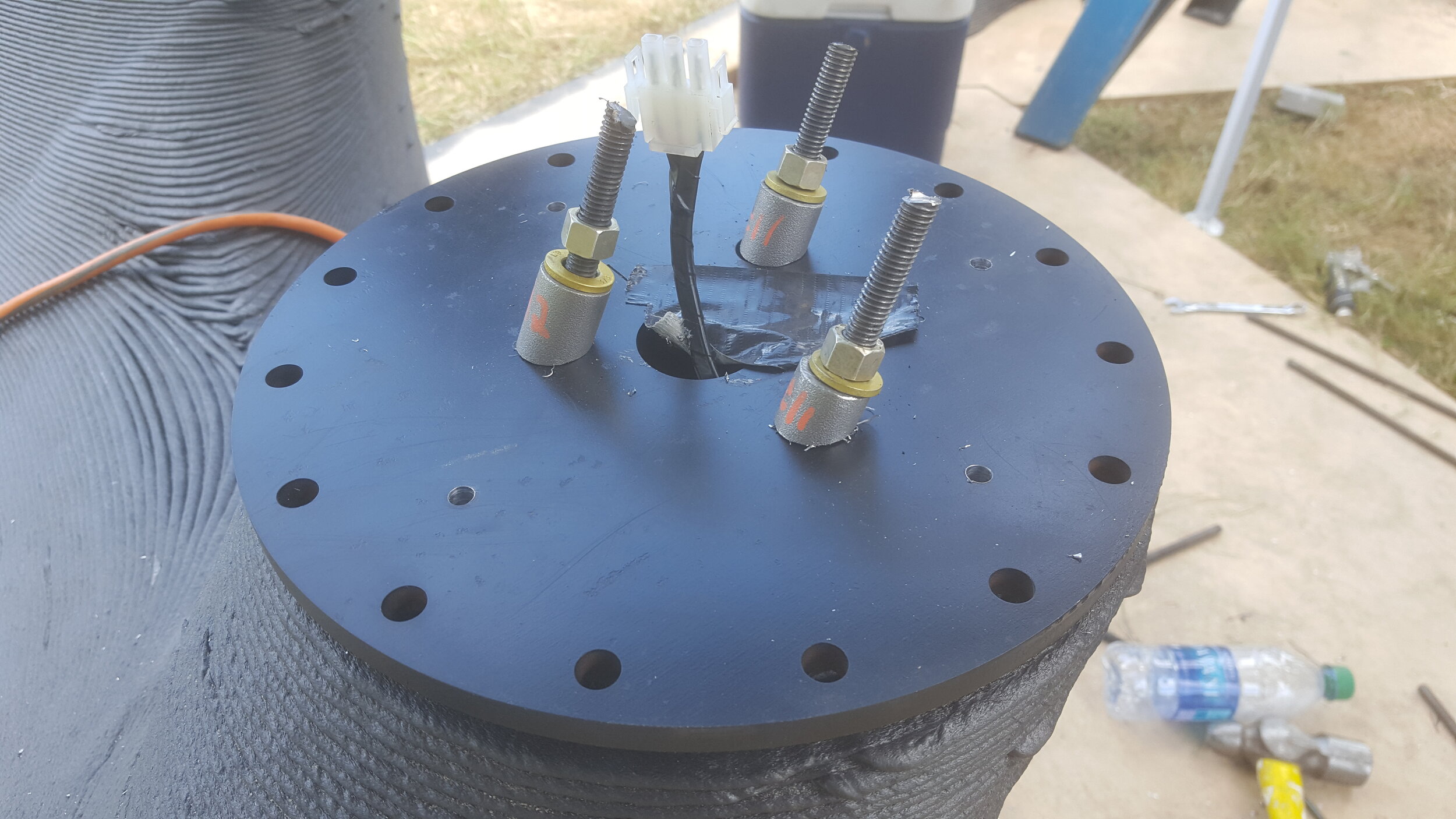
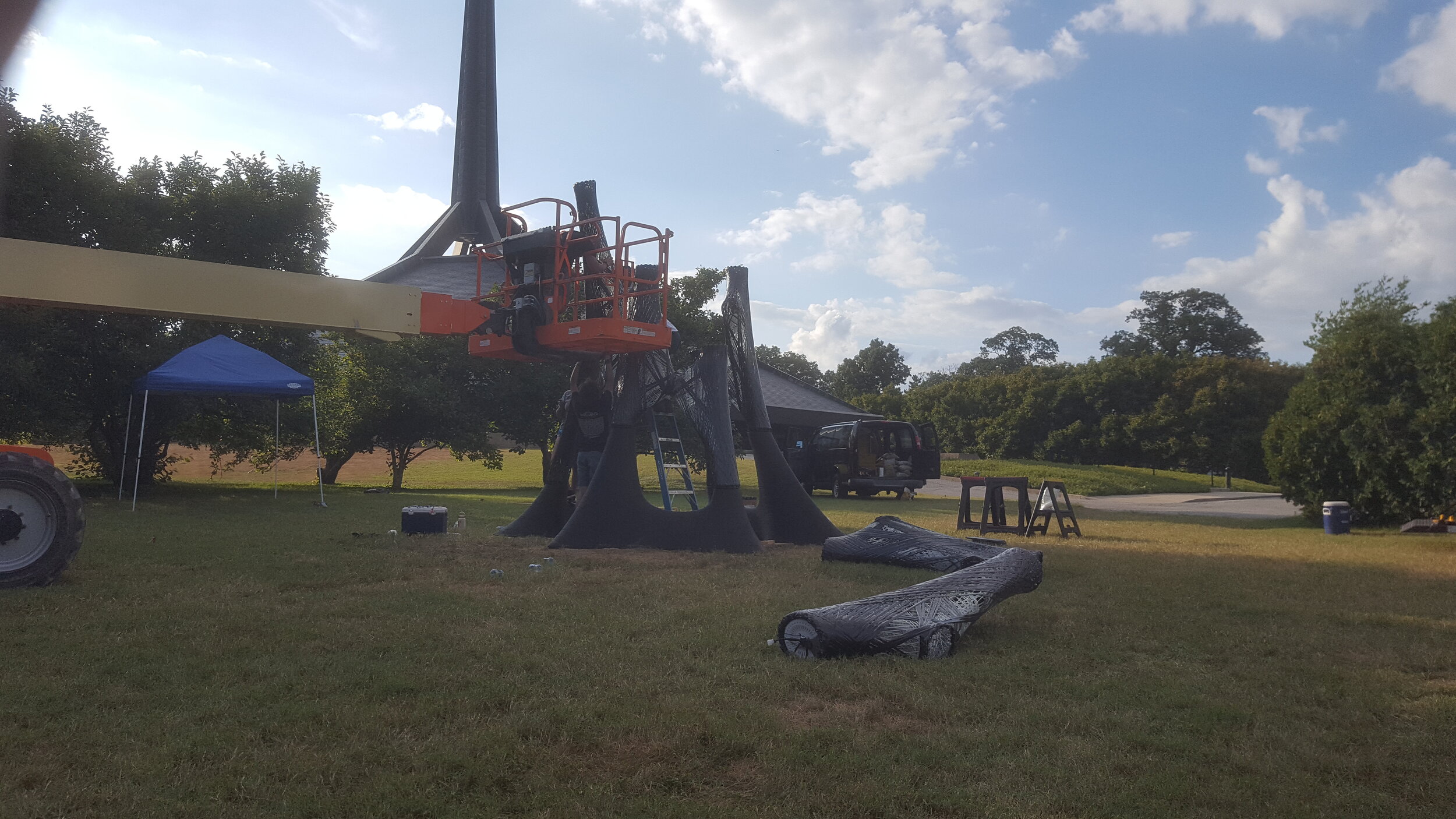
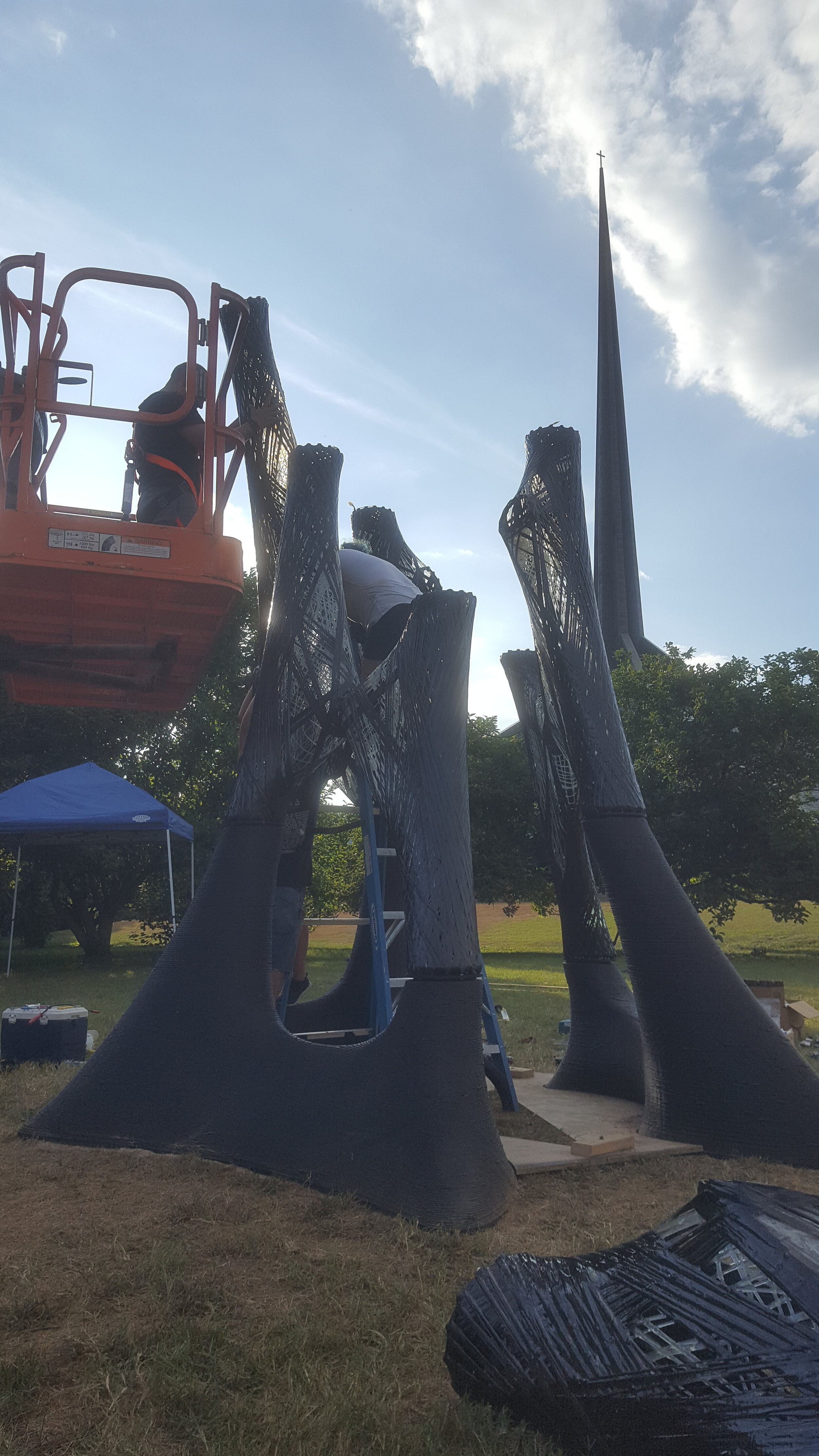

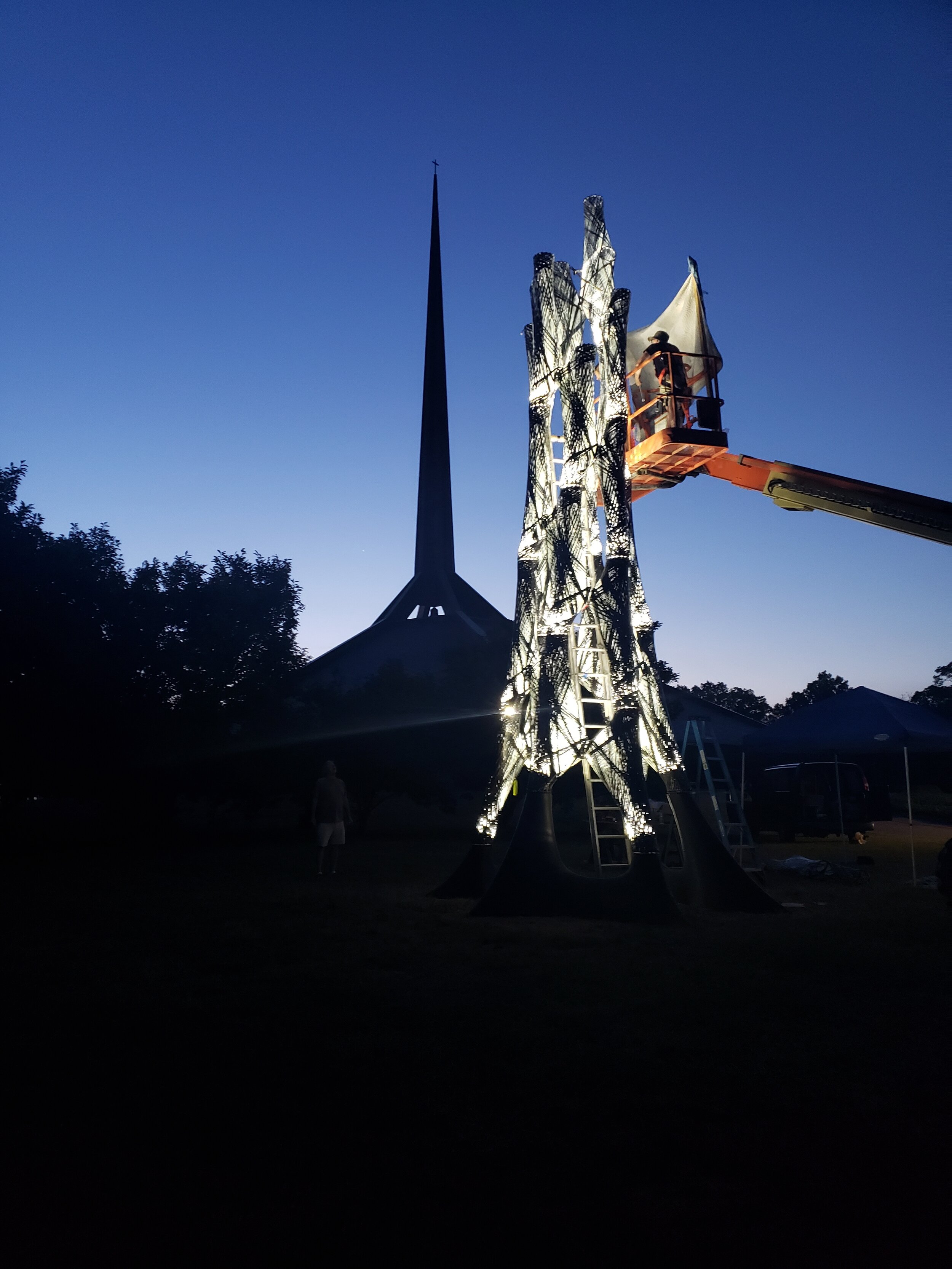
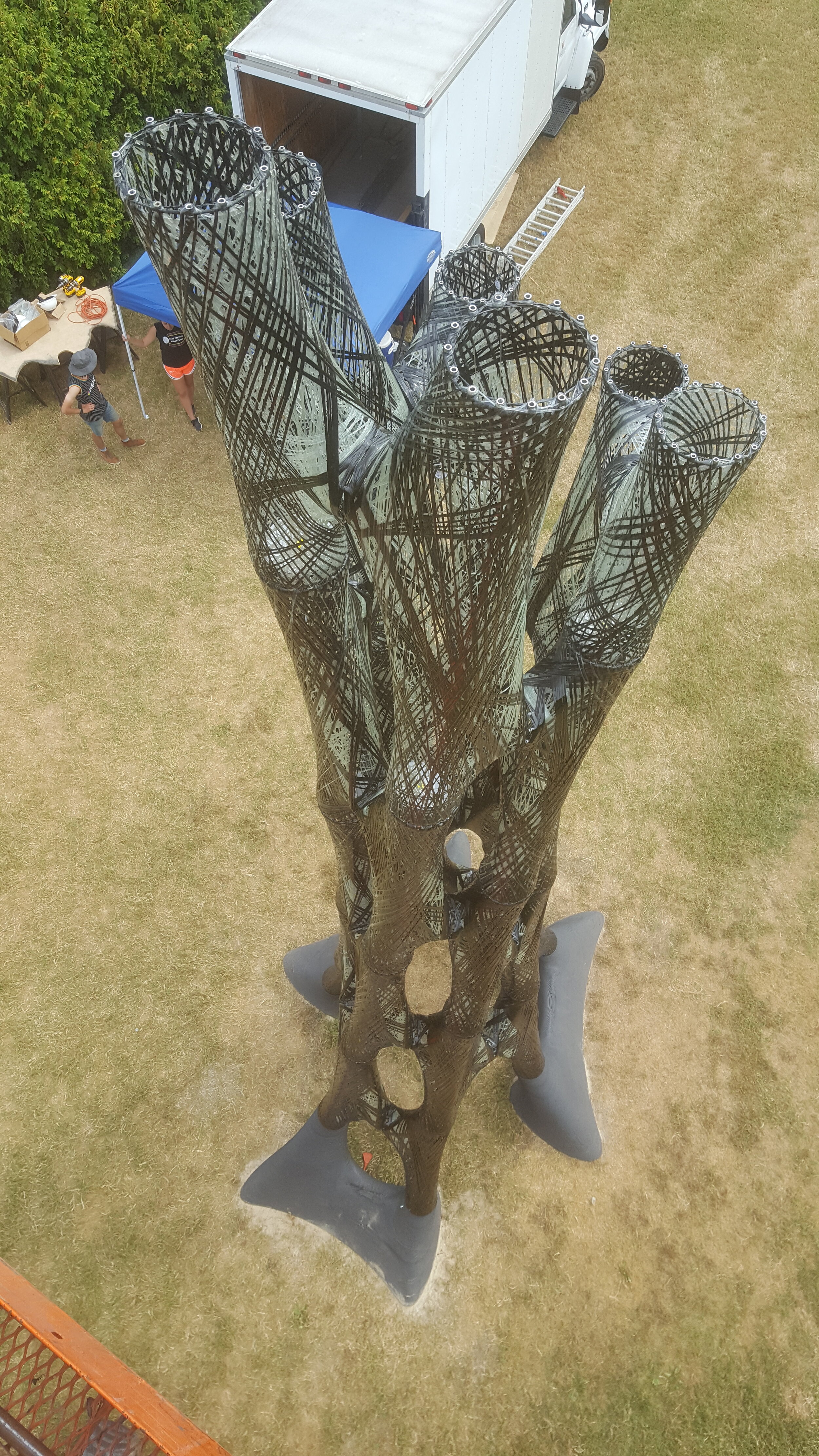
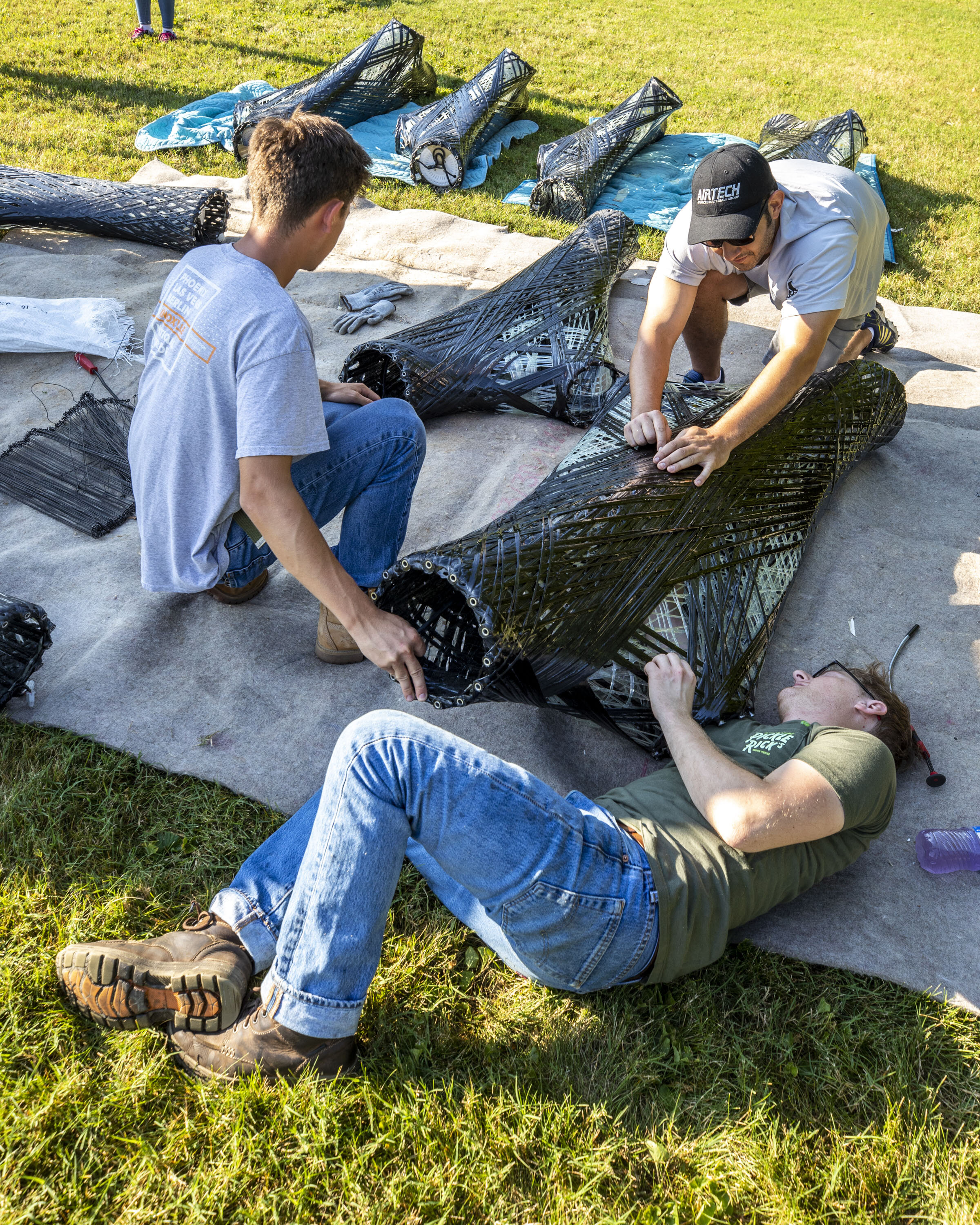
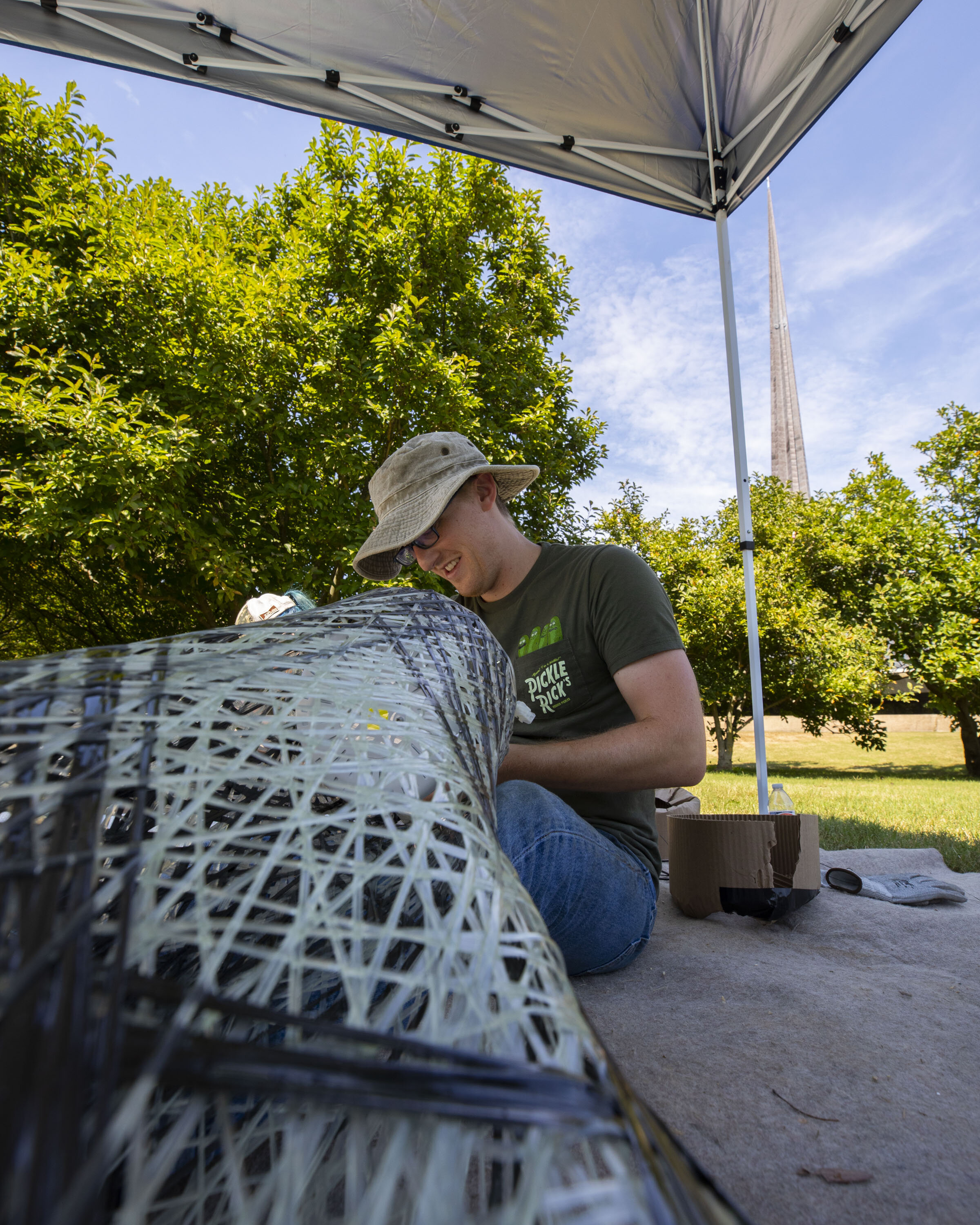
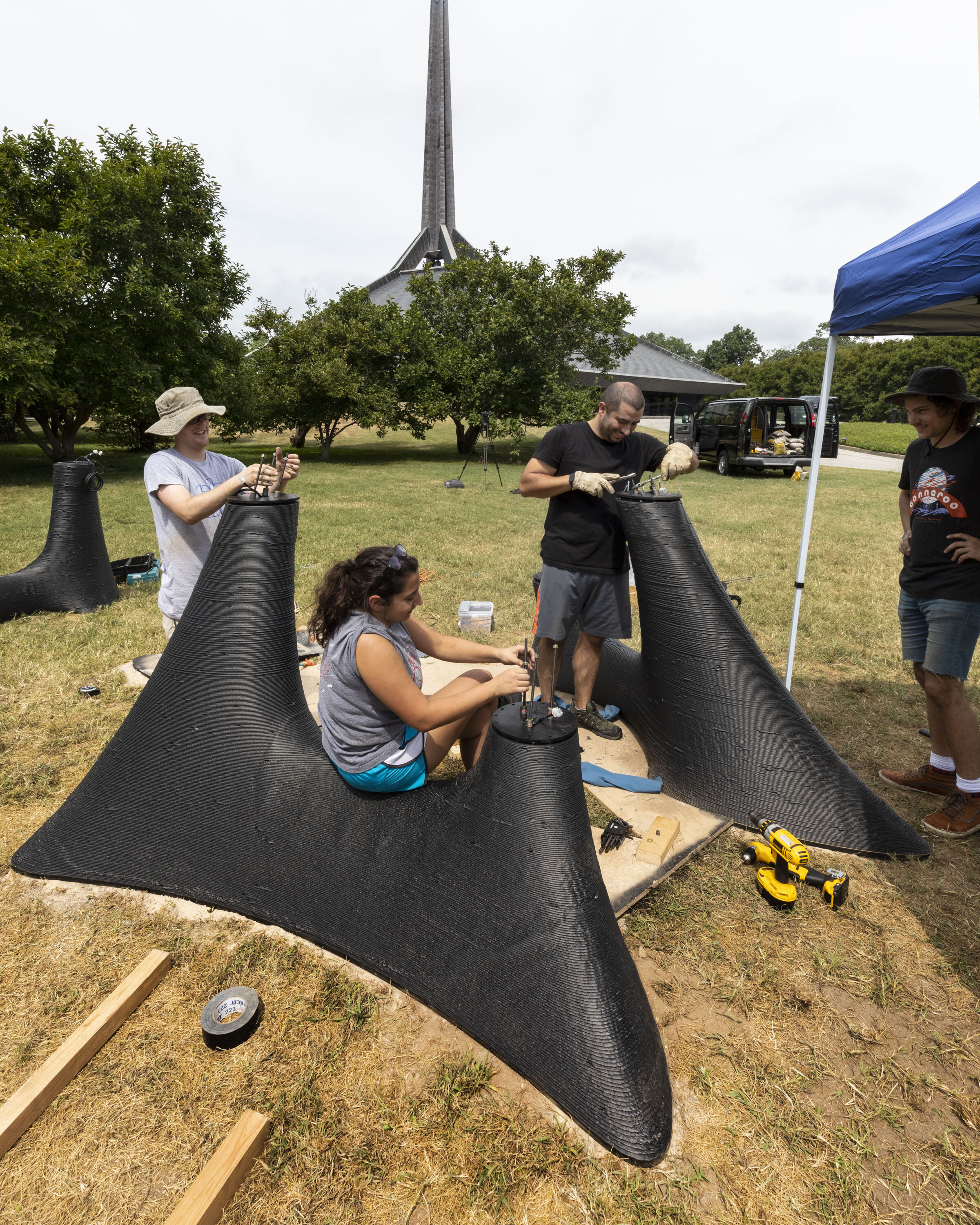
04_Exhibition
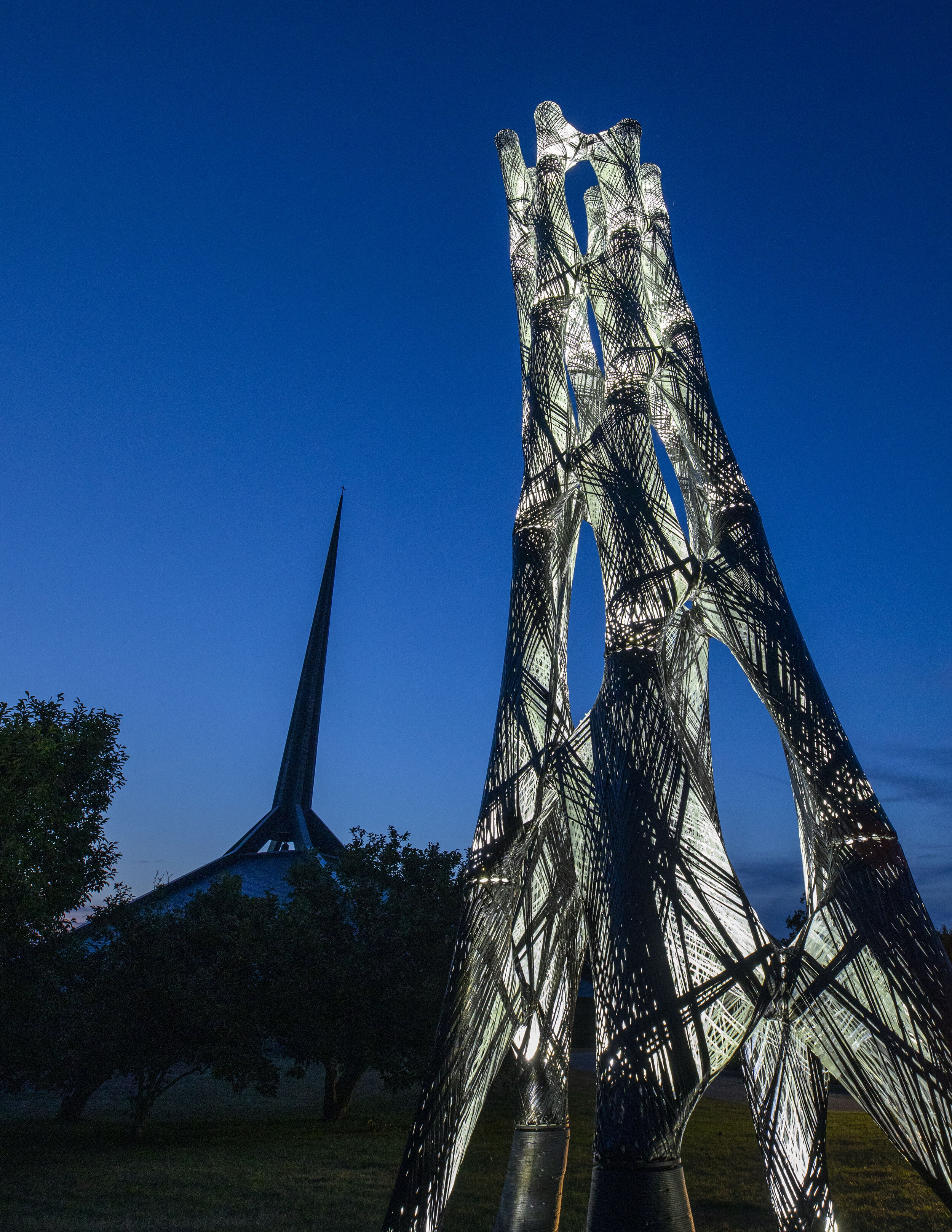
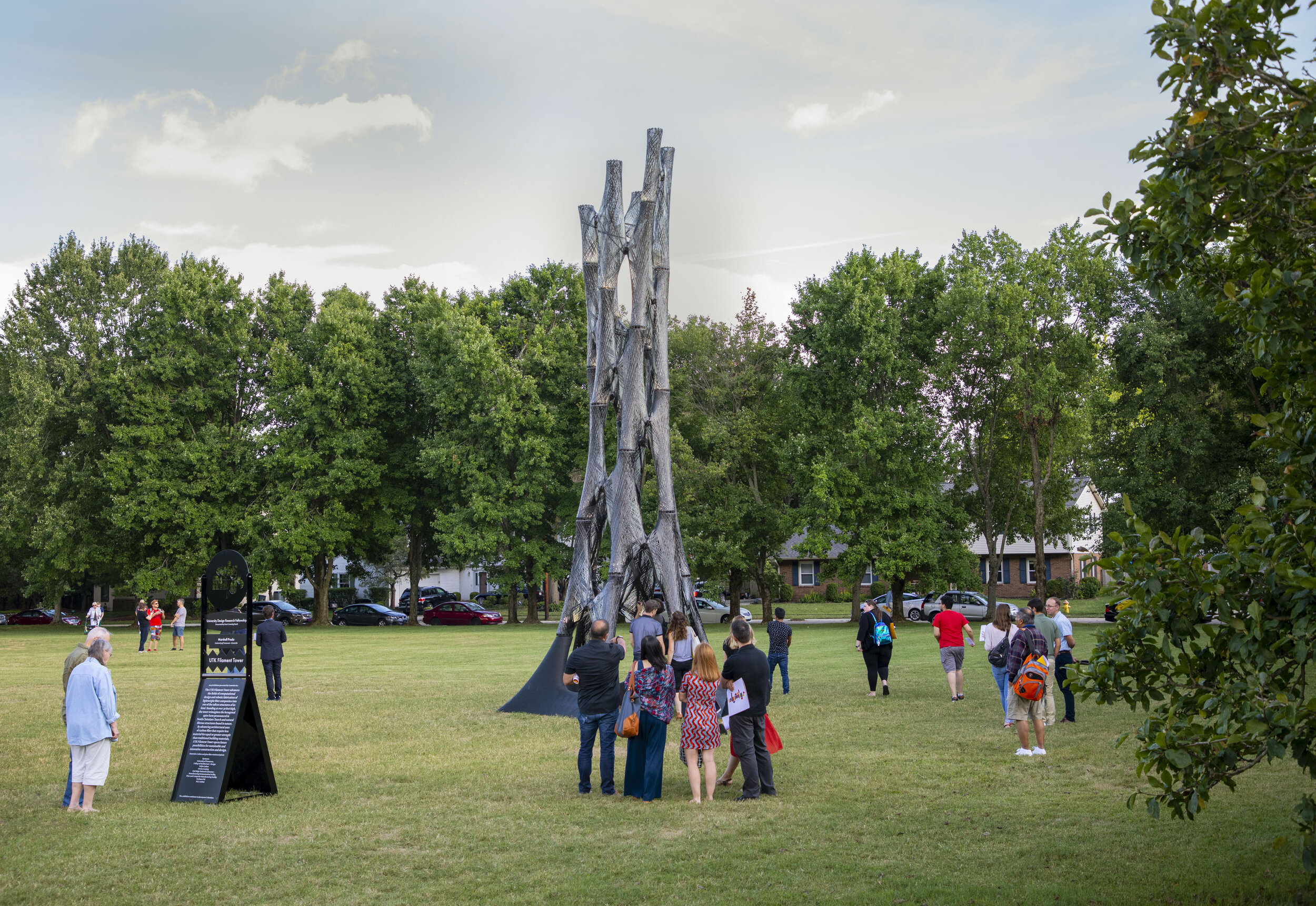

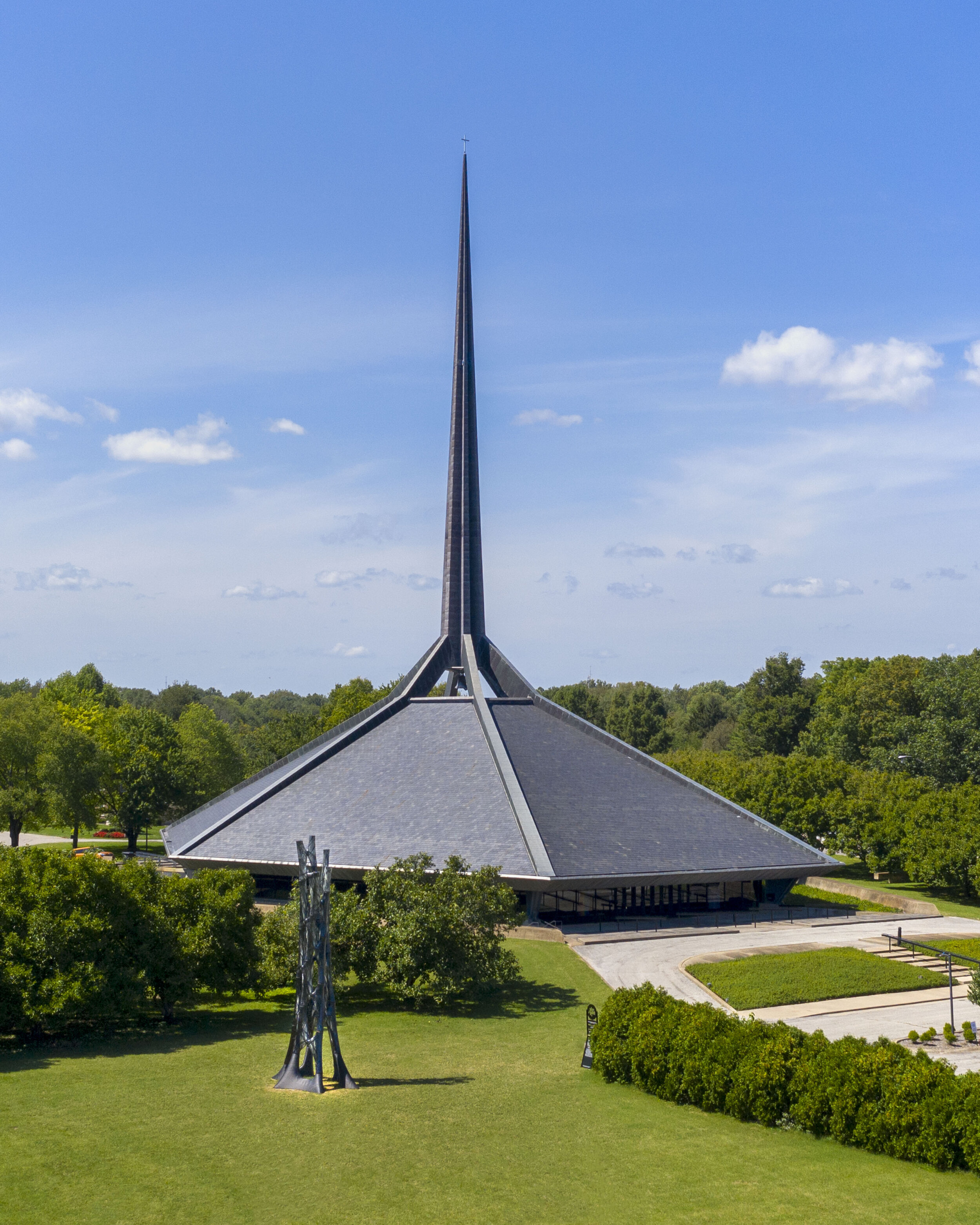
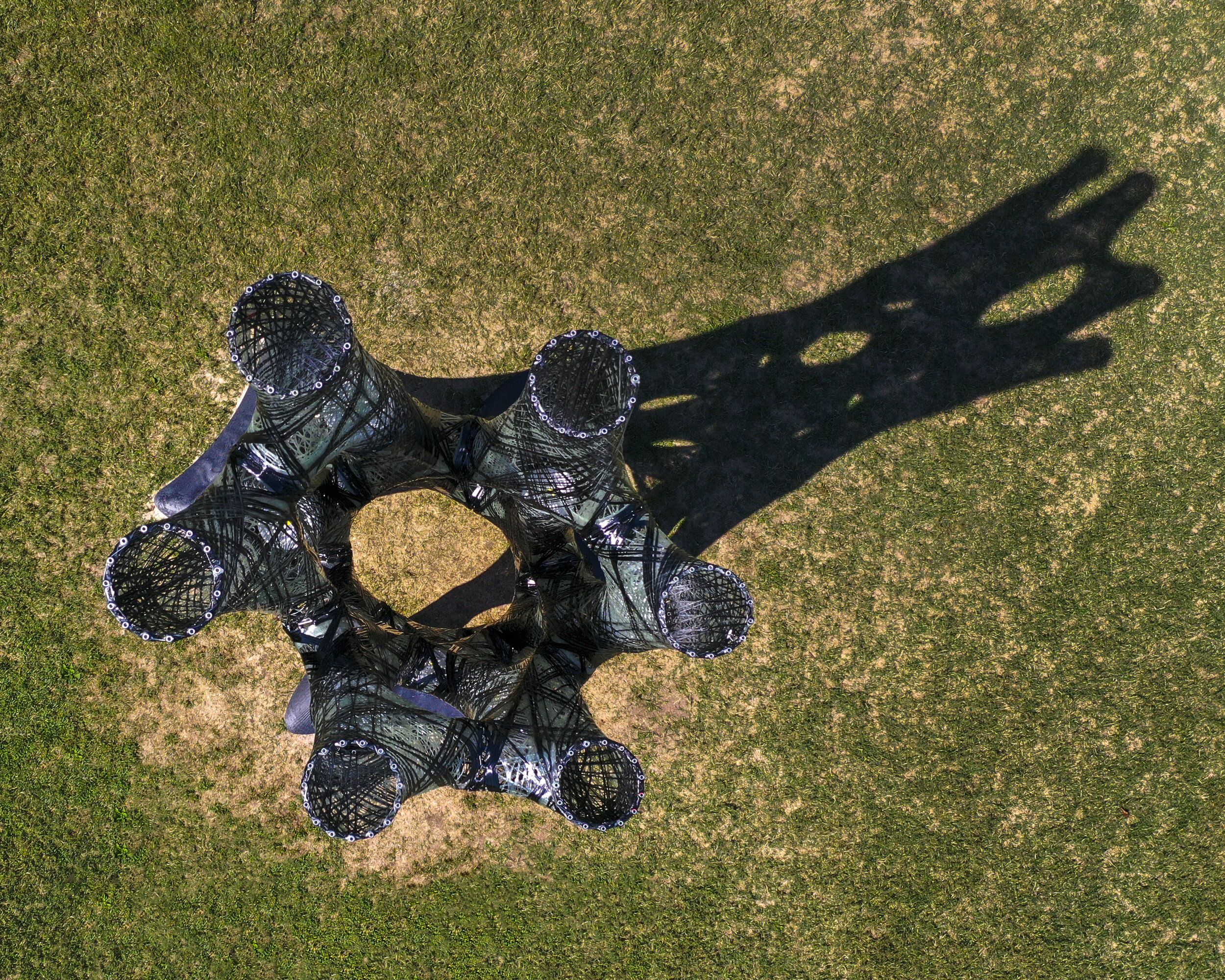
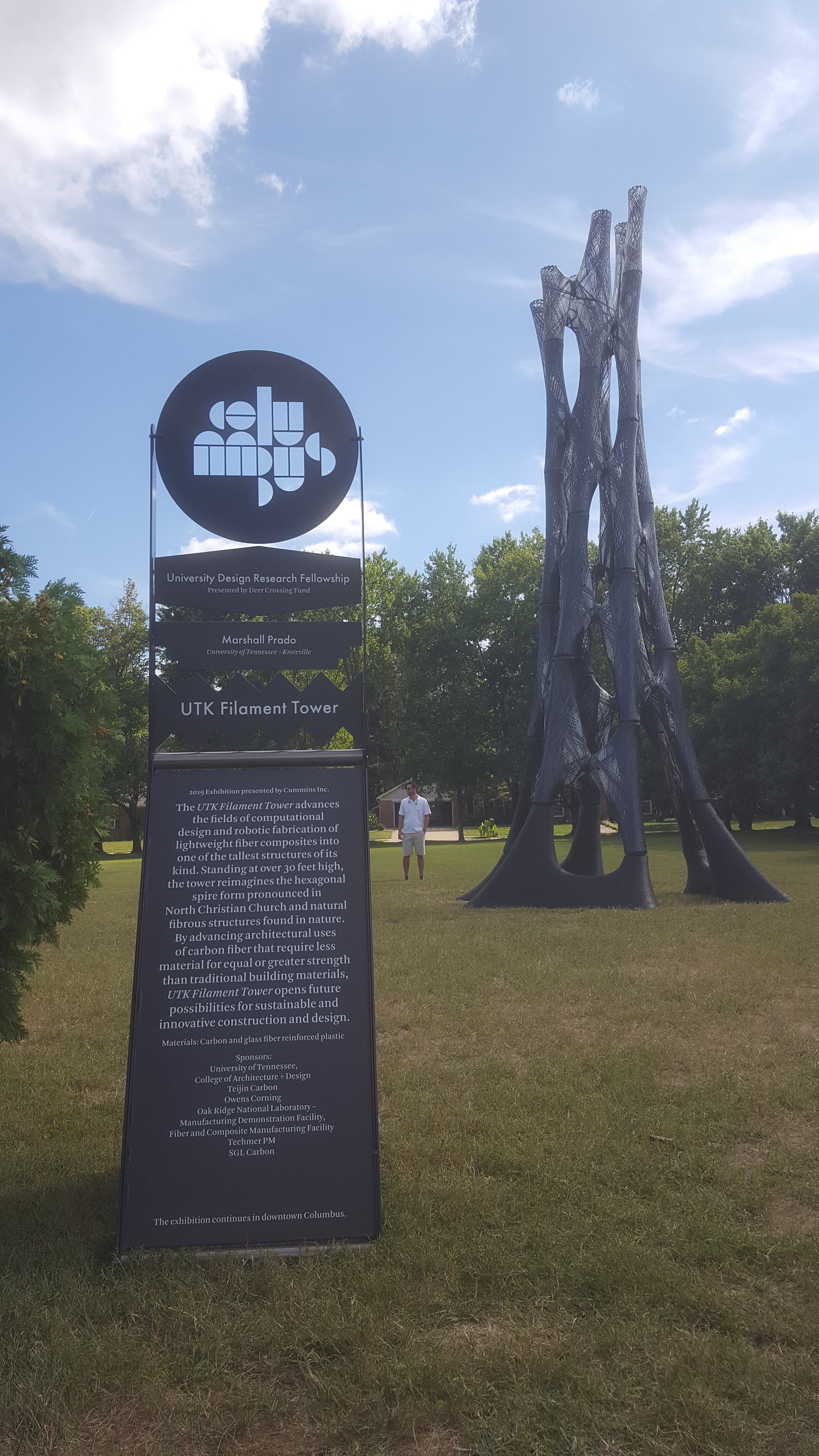
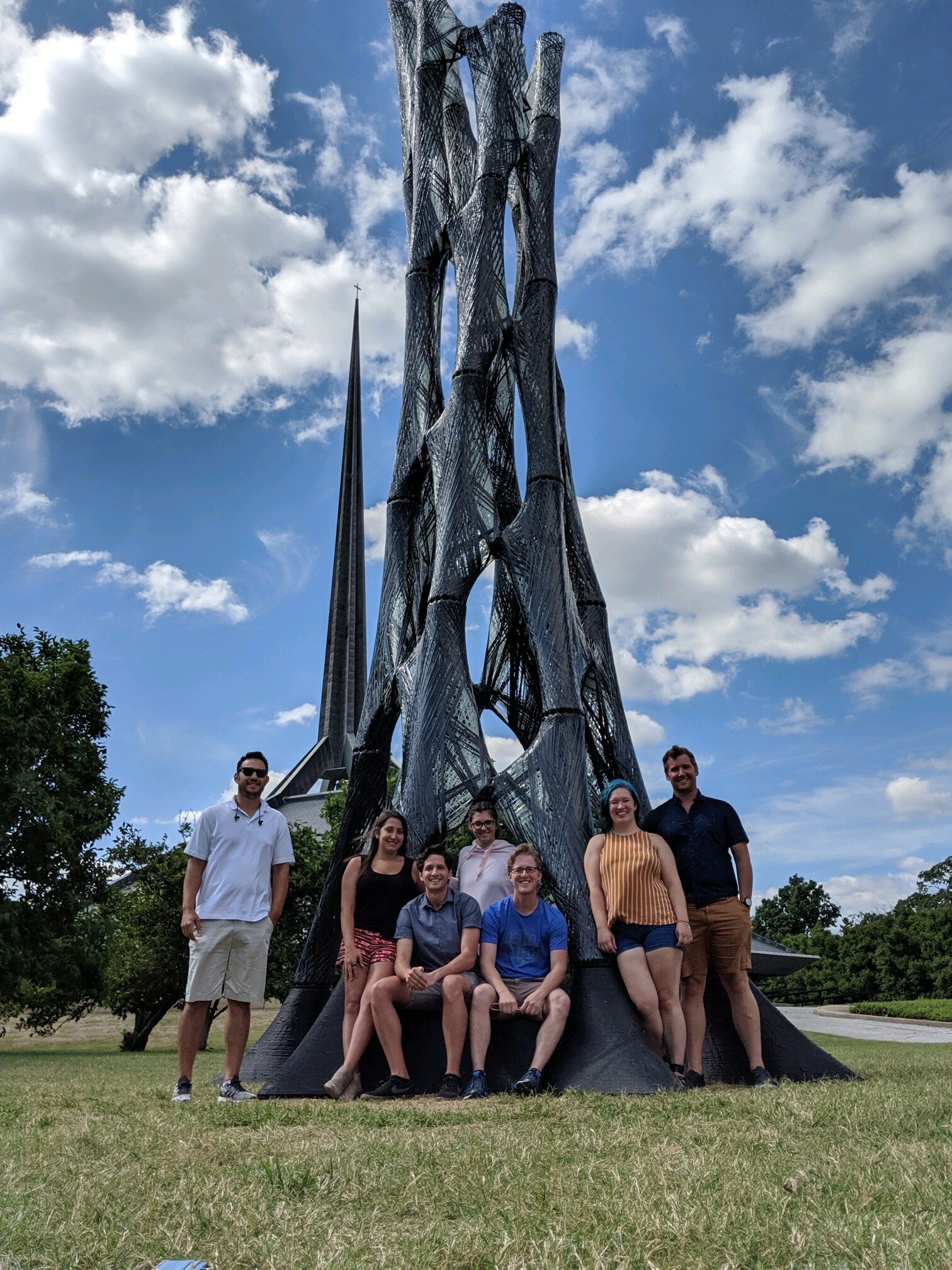
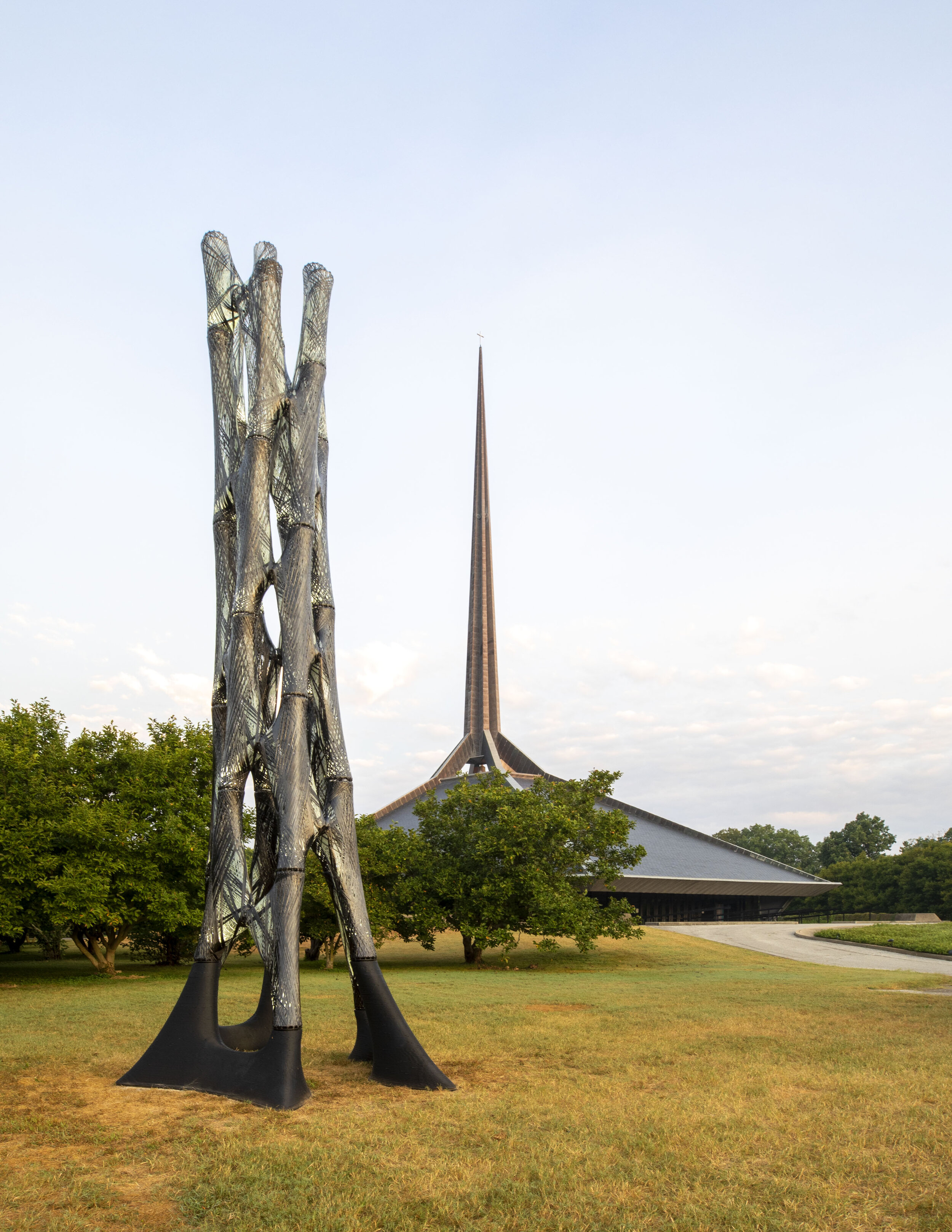
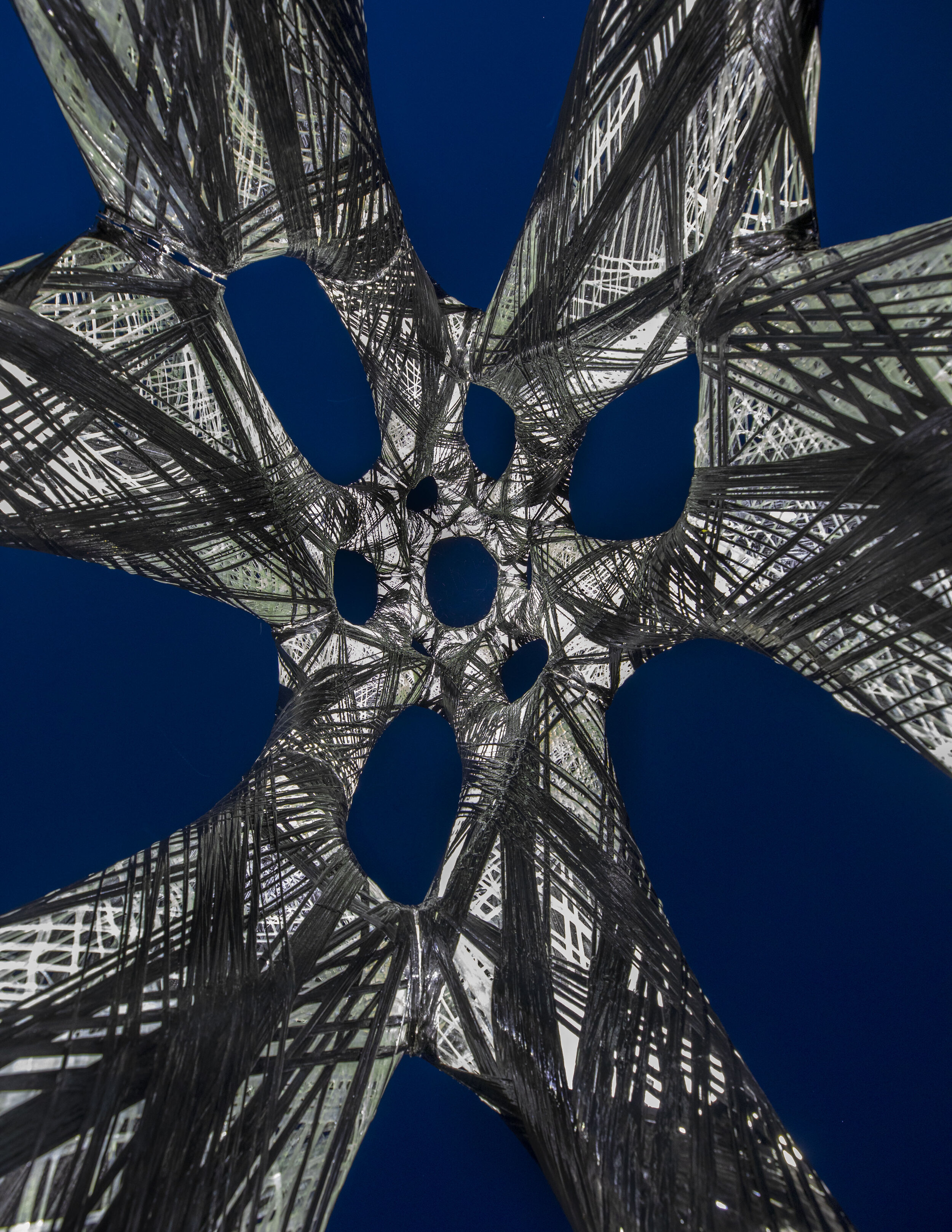
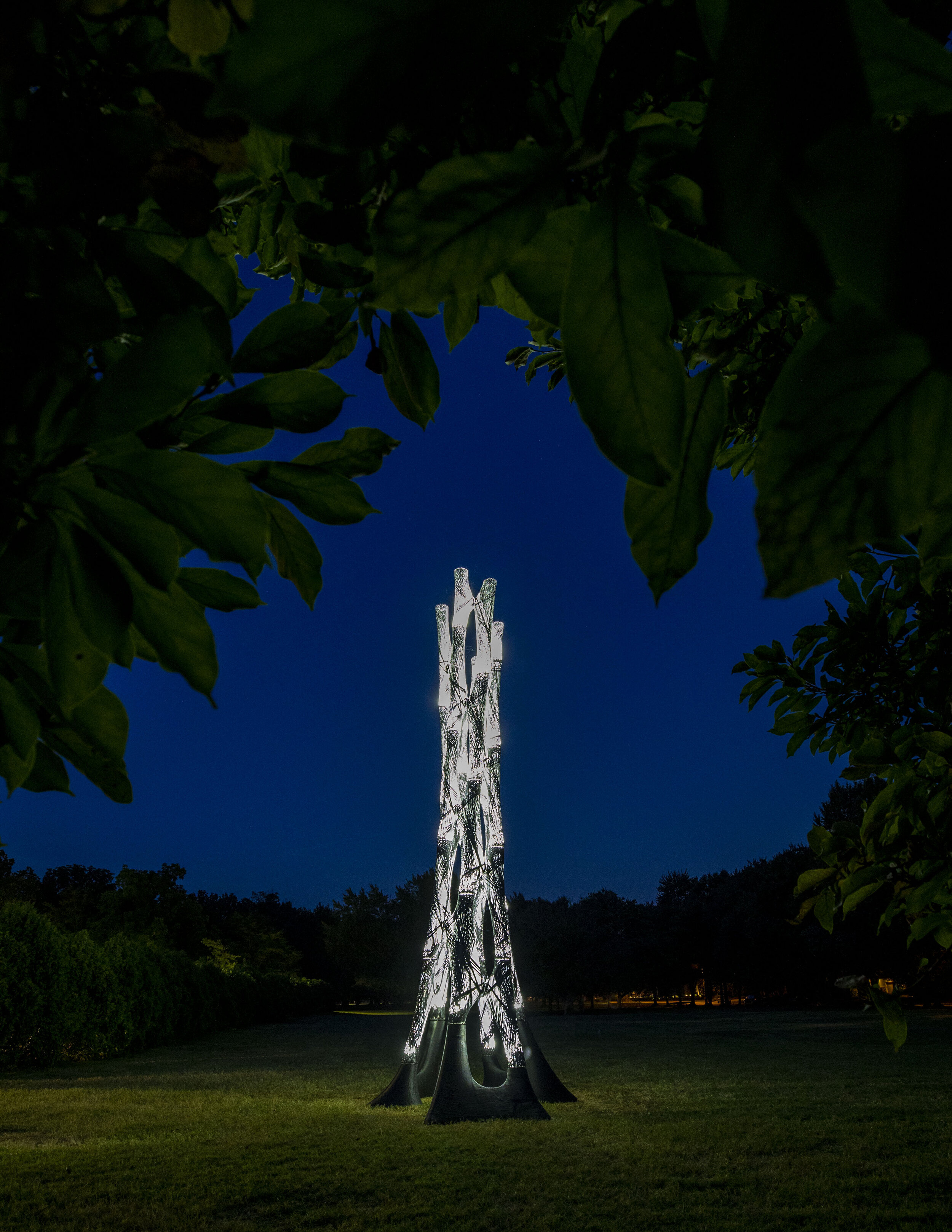